Index
Smart Kitchen: Programmierung einer Webanwendung zur Bedienung von Küchengeräten über den Browser (Frontend mit React.js, Backend mit Node.js) (MA)
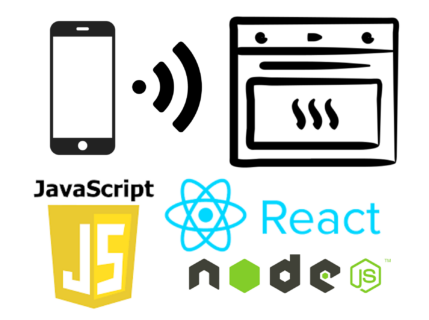
Ausgangssituation
Kochen ist ein Fertigungsprozess, der bisher noch stark von manuellen Verarbeitungsschritten geprägt ist. Besonders die Zubereitung gesunder Mahlzeiten erfordert erheblichen Zeitaufwand, Planung und den Einsatz frischer Zutaten wie Obst und Gemüse, was im hektischen Alltag oft vernachlässigt wird. Zwar existieren bereits technische Lösungen, die den Kochvorgang erleichtern (z.B. Thermomix, Nicer Dicer), jedoch unterstützen diese lediglich Teilprozesse der Zubereitung. Die Anwesenheit des Menschen in der Küche für manuelle Zubereitungsschritte bleibt weiterhin unabdingbar. Um den Zeitaufwand beim Kochen weiter zu reduzieren und langfristig eine vollautomatisierte Küche zu ermöglichen, ist eine verstärkte Automatisierung in der Küche erforderlich.
Ein zentraler Aspekt hierbei ist die Möglichkeit, Küchengeräte aus der Ferne zu bedienen. Eine Möglichkeit zur Realisierung ist die Entwicklung einer Web-Anwendung, mit der Nutzer über einen Browser bequem Küchengeräte steuern können (beispielsweise das Einschalten eines Ofens, die Temperatureinstellung und die Überwachung der aktuellen Temperatur über die Web-Oberfläche).
Aufgabenstellung
Das Ziel der Arbeit besteht in der Entwicklung, Programmierung und Implementierung eines Prototyps einer Web-Anwendung zur Bedienung von Küchengeräten über den Browser.
Als Frontend wird eine Website entwickelt, die auf mobilen Endgeräten über den Browser aufgerufen werden kann. Diese Website ermöglicht es den Nutzern, den aktuellen Status von Geräten (wie etwa die Temperatur eines Ofens) abzurufen sowie die Steuerung dieser Geräte vorzunehmen (beispielsweise das Ein- und Ausschalten des Ofens oder die Festlegung der Temperatur). Die Kommunikation zwischen den Geräten und der Anwendung erfolgt dabei über einen MQTT-Broker (Die Anbindung der Küchengeräte selbst (wie z.B. des Ofens) ist NICHT Teil dieser Arbeit). Das Webinterface soll dann auf die MQTT-Daten zugreifen und so die Anzeige und Steuerung der Geräte ermöglichen. Als Framework für die Frontend-Entwicklung wird React.js verwendet.
Die zugehörige Datenbank, in der unter anderem Benutzer und Geräteinformationen gespeichert werden, wird als relationale Datenbank (z.B. MySQL) implementiert. Benutzer müssen sich in der Webanwendung anmelden und erhalten nur Zugriff auf die ihnen zugewiesenen Geräte.
Die Interaktion des Frontends mit der Datenbank erfolgt über ein Backend, welches eine REST-API bereitstellt. Als Framework für die Backend-Entwicklung wird Node.js verwendet.
Der Webserver zur Bereitstellung der Webanwendung, das Backend sowie die Datenbank werden in einer Cloud-Umgebung (z.B. AWS) gehostet, um eine skalierbare und zuverlässige Bereitstellung der Anwendung sicherzustellen.
Die grundlegenden IT-Architekturen, Anforderungen an die einzelnen Komponenten sowie die Datenbankbeschreibung und das ER-Modell sind vorhanden und werden zu Beginn der Arbeit detailliert besprochen, überprüft und bei Bedarf angepasst. Der Fokus der Arbeit liegt anschließend auf der Programmierung des Frontends mit React.js, der Programmierung des Backends mit Node.js sowie der Bereitstellung der Anwendung in der Cloud.
Deine Tätigkeiten
- Durchdringen der Aufgabenstellung und Einarbeitung in das bestehende Konzept
- Erstellung eines Mockups für das Frontend (z.B. mit Adobe XD oder Figma; im ersten Schritt wird nur ein Interface für mobile Endgeräte erstellt)
- Programmierung des Backends (REST-API) mit Node.js
- Programmierung des Frontends (Web-App) mittels React.js
- Dokumentation der Arbeitsergebnisse und Ausblick auf mögliche Weiterentwicklungen
Deine Fähigkeiten
- Fundierte Programmierkenntnisse in JavaScript, HTML, CSS zwingend notwendig
- Erfahrung in der Entwicklung von Web-Anwendungen (idealerweise mit React.js) zwingend notwendig
- Praktische Erfahrung mit SQL-Datenbanken zwingend notwendig
- Erfahrung mit Websockets/MQTT erwünscht
- Erfahrung mit Cloud-Diensten wie AWS erwünscht
Bewerbung
- Selbständige und gewissenhafte Arbeitsweise
- Regeltermine finden per Teams sowie am FAPS-Standort in Nürnberg “Auf AEG” (Fürther Straße 246b, 90429 Nürnberg) statt
- Studiengänge: Informatik, Mechatronik, Maschinenbau, WING
- Bewerbungen per E-Mail mit Lebenslauf und aktueller Fächerübersicht an andreas.morello@faps.fau.de
Ansprechpartner:
[Extern / MA] Modellierung und Deployment für die datengetriebene Prozessregelung (Data-driven Control / Machine Learning Control) der Wellpappenherstellung
Ausgangslage
Wellpappe hat eine zentrale Bedeutung als Ausgangsmaterial für die Verpackung von Gütern und weist ein hohes jährliches Produktionsvolumen i.H.v. 55 Mrd. m² in Europa auf. Die BHS Corrugated Maschinen- und Anlagenbau GmbH ist Technologieführer für Produktionsanlagen zur Herstellung und Verarbeitung von Wellpappe.
Aufgrund der Komplexität der Einflussgrößen im Herstellungsprozess und der damit verbundenen Schwierigkeit der physikalischen Prozessmodellierung, bieten sich datengetriebene Verfahren aus dem Bereich des Maschinellen Lernens (ML) zur Systemidentifikation und -optimierung an.
Mögliche Aufgabenstellungen
Die Qualität der hergestellten Produkte soll mittels datengetriebener Verfahren (Data-driven Control / Machine Learning Control) geregelt werden. Die Modellierungs- und Optimierungsansätze bedürfen stetiger Weiterentwicklung, sowie der Steigerung des Reifegrades in Richtung Operationalisierung. Potentielle Forschungsfragen stellen sich daher unter anderem in den Bereichen:
- Systemidentifikation via datengetriebener Prozessmodellierung
- Entwicklung und Optimierung fortgeschrittener Reglerarchitekturen
- Evaluation der Systemperformance und Aufbau einer Monitoringkomponente
- Schritte zur Steigerung des Reifegrades in Richtung Operationalisierung
Anforderungen
Je nach Schwerpunkt der Arbeit und vorbehaltlich der Möglichkeit zur Einarbeitung ergeben sich folgende Anforderungen:
- Programmiererfahrung in Python einschließlich einschlägiger ML-Packages (z.B.: PyTorch (Lightning), sklearn, pandas, streamlit, shiny, MLFlow)
- Grundkenntnisse gängiger Werkzeuge der Softwareentwickung (z.B.: docker, git)
- Grundkenntnisse gängiger Werkzeuge der Datenübertragung und -persistierung (z.B.: MQTT, SQL, NoSQL)
- Kenntnisse in den Grundlagen der Regelungstechnik und / oder Kontrolltheorie
- Interesse an Automatisierungstechnik
- Hohes Sprachniveau in Deutsch oder Englisch in Wort und Schrift
- Selbstständige und strukturierte Arbeitsweise
Bewerbung
Bewerbungen sind per Mail an till.sindel@faps.fau.de zu richten, mit der Bitte um konkretem Bezug auf die Ausschreibung, einen angehängten Lebenslauf, sowie die aktuelle Fächerübersicht.
It’s Clusterin’ Time! Realisierung eines Mixed-SBC-Clusters für die Edge (BA/PA/MA)
Der Einsatz von Edge Computing gewinnt in vielen Bereichen an Bedeutung, da er die Datenverarbeitung näher an den Ort der Datenentstehtung verlagert. Ein Mixed-SBC-Cluster, der verschiedene Single Board Computer (SBC) wie Nvidia Jetson und Raspberry Pi umfasst, bietet eine ausgezeichnete Plattform, um die Herausforderungen und Möglichkeiten des Edge Computings zu erproben und zu demonstrieren.
Ziel ist die Entwicklung Mixed-SBC-Clusters für die Edge, der als experimentelle Plattform in industrienaher Forschung und für Lehrzwecke im Automatisierungsumfeld dient. Dieser Cluster soll die Heterogenität realer IT-Infrastrukturen widerspiegeln und das Sammeln praktischer Erfahrungen mit Cluster-Management, verteilten Speichersystemen und der Integration von Erweiterungsmodulen (z.B. Funkmodul, Neural Processing Unit und FPGA) eröffnen.
Schwerpunkte der Arbeit:
- Aufbau und Konfiguration eines heterogenen SBC-Clusters für Edge Computing Szenarien.
- Einsatz eines Cluster-Management-Systems und Implementierung eines Service Mesh.
- Einsatz von Automatisierungswerkzeugen und Infrastruktur-as-Code (IaC) zur effizienten Verwaltung und Konfiguration.
- Integration von Storage-Lösungen und spezifischen Erweiterungsmodulen für verschiedene Anwendungsfälle.
- Integration in Anwendungsfälle der Automatisierungstechnik in industriellen Produktionsanlagen, der Gebäudeautomatisierung und insbesondere des Energiemanagements.
- Beitrag zum Transfer in die Lehre als Praktikumsversuch oder Übungseinheit
Weitere Informationen erhalten Sie auf Anfrage, der Arbeitsumfang kann entsprechend der Arbeit angepasst werden und die Bearbeitung weitestgehend im Home-Office stattfinden.
Entwicklung von Geschäftsmodellen für neue Smart-Energy-Management-Funktionalitäten
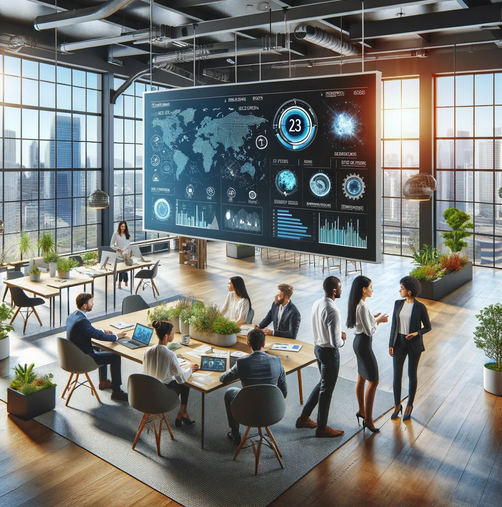
Hintergrund: Im Zuge des fortschreitenden Wandels in der Energiebranche und der zunehmenden Bedeutung von nachhaltigen und effizienten Energiemanagementsystemen, bieten sich für innovative Startups vielfältige Möglichkeiten. Diese Abschlussarbeit zielt darauf ab, den Grundstein für ein solches Startup zu legen, indem sie innovative Geschäftsmodelle für neue Energiemanagementfunktionalitäten entwickelt.
Thema: Entwicklung von Geschäftsmodellen für neue Energiemanagementfunktionalitäten mit dem Ziel der Gründung eines Startups.
Mögliche Aufgaben:
- Analyse aktueller Trends und Herausforderungen in der Energiebranche, insbesondere im Bereich Energiemanagement.
- Identifikation und Bewertung neuer Technologien und Funktionalitäten im Energiemanagement.
- Entwicklung innovativer Geschäftsmodelle, die diese neuen Funktionalitäten nutzen.
- Erstellung eines umfassenden Businessplans, einschließlich Marktanalyse, Strategieentwicklung und Finanzplanung.
- Erarbeitung eines Konzepts zur Umsetzung und Skalierung des Startups.
Power-Hardware-in-the-Loop (PHIL) Simulator für industrielle Gleichstromnetze
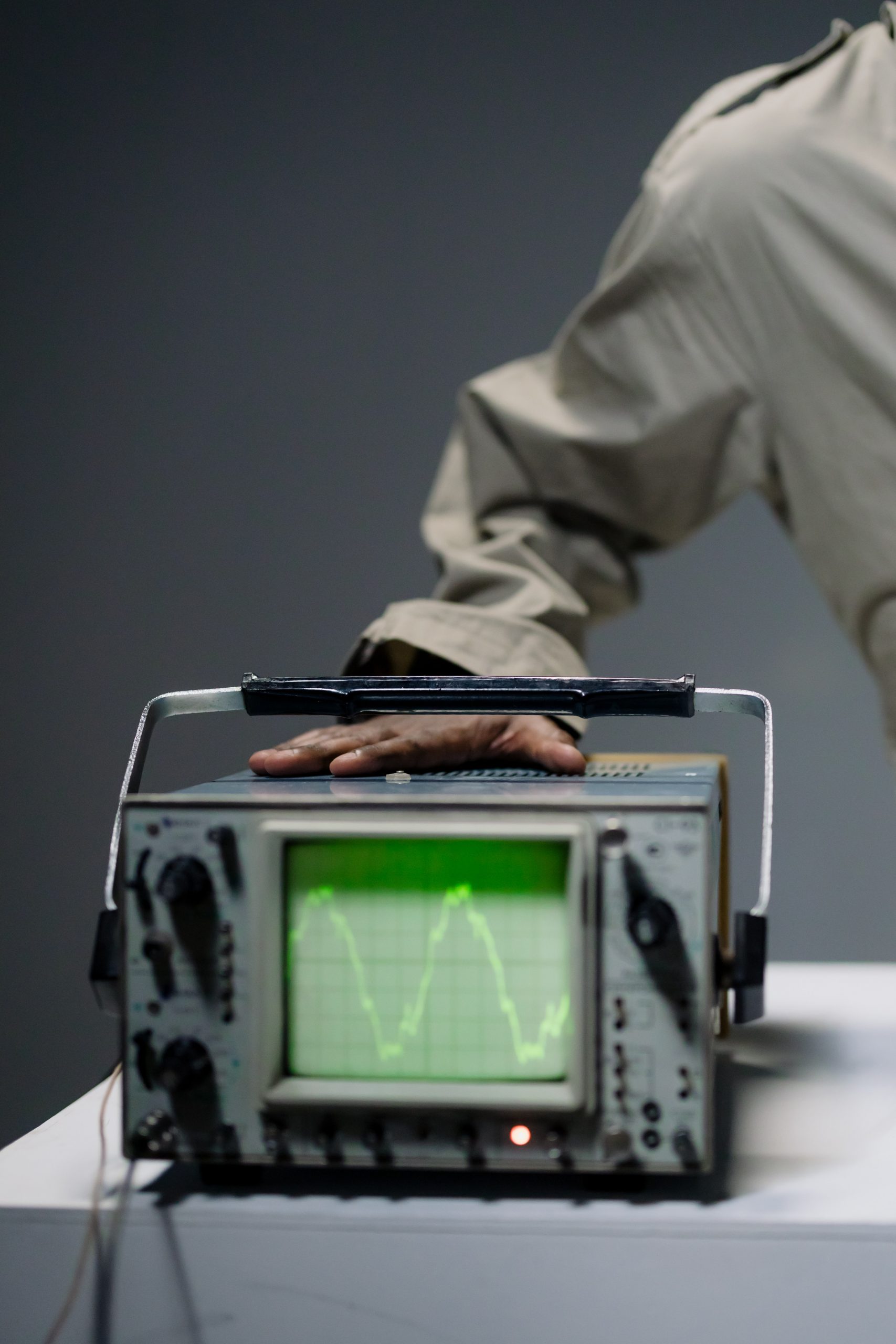
Im Rahmen der Energiewende verlagert sich der Fokus von fossilen Brennstoffen und Atomenergie zu erneuerbaren Energiequellen. Hybride Netzstrukturen aus einer Kombination aus Gleich- und Wechselstrom vereinen die Vorteile beider Versorgungsstrategien. Sie berücksichtigen jede Art von Verbrauchern, Speichern und Erzeugern.
In Kooperation mit über 30 namhaften Partnern der Industrie baut der FAPS in seinen Laborhallen eine Demonstratoranlage mit regenerativen Erzeugern, verschiedenen Speichern und industriellen Verbrauchern auf. Entstandene Simulationen können dort messtechnisch validiert und das Gesamtkonzept auf die praktische Umsetzbarkeit sowie die Wirtschaftlichkeit untersucht werden.
Mit dem neuartigen PHIL-Ansatz sollen Energieverläufe aus Simulationen mit Leistungselektronik verbunden werden, um so Strom- und Spannung als Quelle und als Senke an einem Gleichstromnetz aufzuschalten.
Für Abschlussarbeiten ergeben sich folgende Anknüpfungspunkte:
- Stand der Technik und Forschung im Bereich PHIL und Möglichkeiten der PHIL-Simulation
- Entwicklung eines PHIL-Simulators durch Kopplung von Simulationsumgebung und Netzteil
- Entwicklung einer Bibliothek (z. B. MATLAB), um Signalverläufe vorzugeben
- Messung realer Leistungsverläufe von Produktionszellen, einzelnen Verbrauchern, regenerativen Erzeugern oder Verbrauchern, um diese in die Bibliotheken zu übernehmen
- Implementierung eines messtechnischen Feedbacks an die Simulationsumgebung z. B. mit interoperablen I4.0 Kommunikationsprotokollen (OPC UA, MQTT etc.)
Entwicklung eines Messkoffers/Messkonzeptes zum Nachweis des CO2-Fußabdrucks
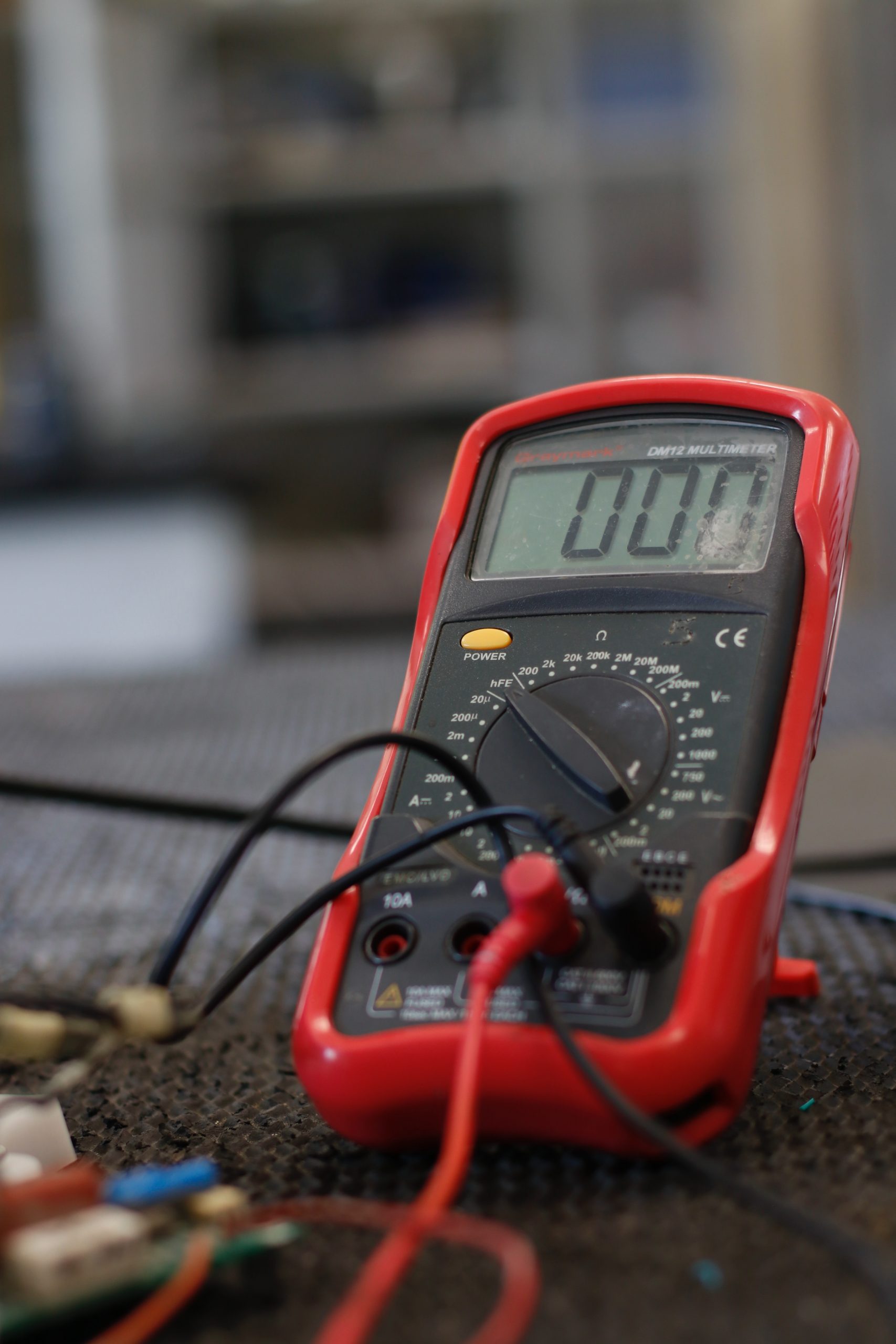
Um den CO2-Fußabdruck eines Produkts/einer Fertigungslinie gegenüber Verbrauchern, Kunden oder Regulierungsbehörden nachzuweisen und mit ihren Lieferanten gezielte Reduktionsmaßnahmen zu initiieren, sind Unternehmen auf genaue Informationen auf Produktebene angewiesen. Der CO2-Fußabdruck ist schon längst kein Imagefaktor für Unternehmen mehr, sondern stellt bereits ein signifikantes Kaufargument in vielen Industriesparten wie zum Beispiel in der Automobilindustrie dar oder wird politisch bereits gefordert. Mit einem neuartigen Messkoffer soll Unternehmen eine Hilfe gegeben werden, wie die CO2-Emissionen ermittelt und nachverfolgt werden können. Aufbauend darauf können Reduzierungsmaßnahmen zur Dekarbonisierung entwickelt und ergriffen werden.
Mögliche Abschlussarbeiten/Inhalte:
- Grundlagenrecherche zur Bestimmung oder Zertifizierung des CO2-Fußabdrucks von Produkten, Produktionsanlagen, Werken oder digitalen Services etc.
- Identifikation und Beurteilung aller Einflüsse auf den CO2-Fußabdrucks und Generierung von Kennzahlen (auch wirtschaftlich)
- Grundlagenermittlung für einen Messkoffer/ein Messkonzept und Ansprüche an die Sensorik und Auswertung
- Bau und Verdrahtung des Messkoffers oder/und Programmierung von Auswerteeinheiten und User-Interface (z. B. SPS, Computer, Messkarten, Mikrocontrollern, Webserver etc.)
- Recherche zu bestehenden Softwarelösungen/Messkonzepten
- Möglichkeiten der Kopplung mit Industriesteuerungen (z. B. SPS oder Cloud-Edge-Devices)
- Aufzeigen von Maßnahmen zur Reduzierung des CO2-Fußabdrucks zur Dekarbonisierung von Produktionsanlagen/Werken etc.
- Ggf. Simulationskopplung
Digitaler Zwilling zur Bestimmung des CO2-Fußabdrucks
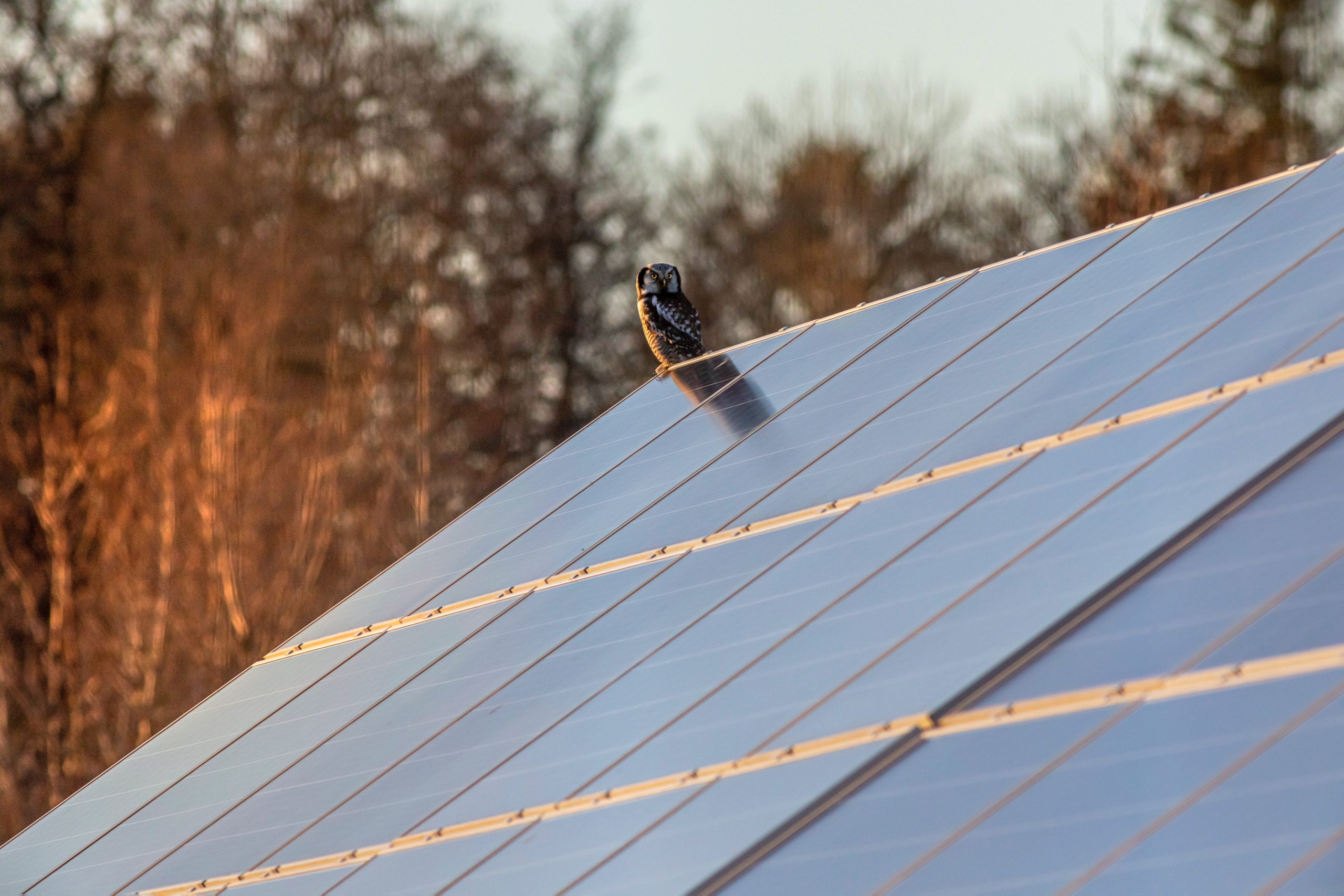
Um den CO2-Fußabdruck eines Produkts/einer Fertigungslinie gegenüber Verbrauchern, Kunden oder Regulierungsbehörden nachzuweisen und mit ihren Lieferanten gezielte Reduktionsmaßnahmen zu initiieren, sind Unternehmen auf genaue Informationen auf Produktebene angewiesen. Der CO2-Fußabdruck ist schon längst kein Imagefaktor für Unternehmen mehr, sondern stellt bereits ein signifikantes Kaufargument in vielen Industriesparten wie zum Beispiel in der Automobilindustrie dar oder wird politisch bereits gefordert.
Mögliche Abschlussarbeiten/Inhalte:
- Grundlagenrecherche zur Bestimmung oder Zertifizierung des CO2-Fußabdrucks von Produkten, Produktionsanlagen, Werken oder digitalen Services etc.
- Identifikation und Beurteilung aller Einflüsse auf den CO2-Fußabdrucks
- Simulationstechnische Lösungen (z. B. Digital Twin) zur Berechnung des Carbon-Footprints aus den Energieflüssen z. B. von Produktionsanlagen
- Tracking/Transparenzbildung des Carbon-Footprints über den gesamten Produktlebenszyklus
- Aufzeigen von Maßnahmen zur Reduzierung des CO2-Fußabdrucks zur Dekarbonisierung von Produktionsanlagen/Werken etc.
BA/MA – Deep Learning for Time Series Signals for Anomaly Detection and Monitoring of Injection Molding Machines
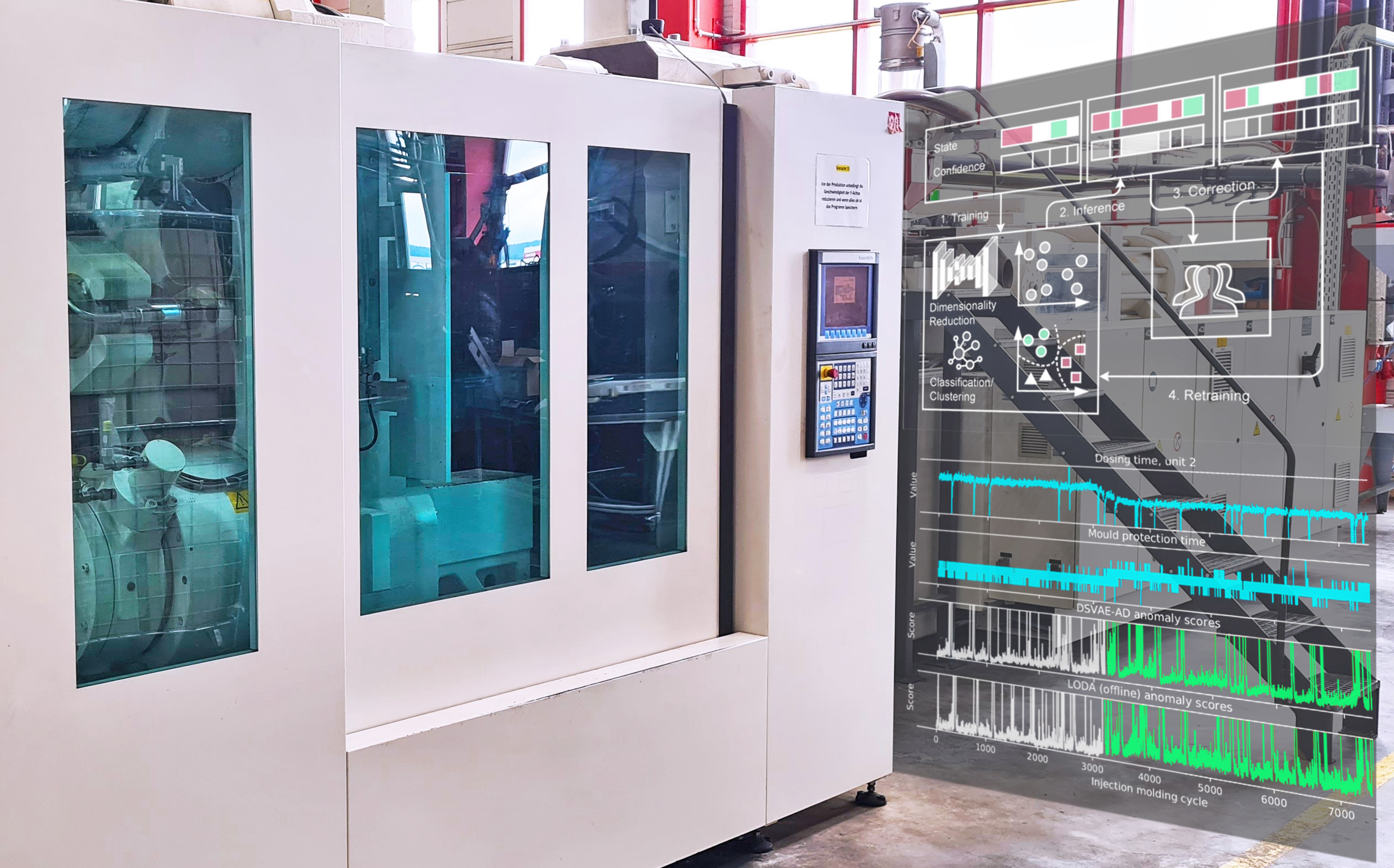
Ausgangssituation:
Das Spritzgussverfahren ist branchenübergreifend eines der wichtigsten Fertigungsverfahren zur kosteneffizienten Produktion großer Stückzahlen von Bauteilen. Moderne Spritzgussmaschinen weisen vielfältige Sensoren zur Erfassung von Betriebsdaten auf. Standardisierte Kommunikationsprotokolle (OPC UA, MQTT) erlauben die einfache Integration weiterer Sensorik zur vollumfänglichen digitalen Abbildung des Maschinenbetriebes. Zur Auswertung der erfassten Daten stehen Methoden des maschinellen Lernens zur Verfügung. Diese lassen automatisiert Rückschlüsse auf die Prozess- und Produktqualität, ohne einer aufwendigen Interaktion mit den menschlichen Anwender zu. Sie erlauben des Weiteren die Erzeugung von Prognosen über die Entwicklung von Messwerten, welche die Grundlage zur Realisierung einer bedarfsgerechten Wartung (Predictive Maintenance) darstellen.
Bei Spritzgussmaschinen kommen Messgrößen wie bsp. Forminnendruck, Dosierzeit oder Wasserdurchflussmenge standardmäßig eine besondere Bedeutung zu. Hinzu kommt mit modernen Systemen der Körperschall. Geeignet ausgewertet, können diese Parameter die Grundlage zur Effizienzsteigerung des Maschinenbetriebs darstellen. Sie erlauben eine Werkzeugoptimierung durch die Vorhersage von Wartungsintervallen, die Optimierung der Werkzeugparameter, eine Entlüftungskontrolle und eine Verschleißkontrolle.
Keywords:
I 4.0, Predictive Maintenance, Injection Moulding, Machine Learning, Process Engineering &
Monitoring, Acoustic Emissions
Aufgabenstellung:
- Analyse am Markt verfügbarer Predictive Maintenance Systeme für Spritzgussmaschinen
- Begleitung und Dokumentation der Einführung eines der Systeme
- Datenauswertung: Vergleich zwischen beobachteten physikalischen Effekten und den
Signaländerungen - Erarbeitung übertragbarer Lösungskonzepte und Methoden (Standardisierung)
- Wirtschaftlichkeitsbetrachtung anhand der identifizierten Optimierung
- Prototypische Validierung des erarbeiteten Lösungsansatzes
- Dokumentation der Arbeit
Anforderungsprofil:
- Student der Fachrichtung Ingenieurwissenschaften
- Programmierkenntnisse in einer Hochsprache (z.B. Python, C++, C#, Java, Matlab)
- Kenntnisse der physikalischen Grundlagen von Sensoren und Signalverarbeitung
- Gute Kommunikationsfähigkeit
- Verhandlungssicheres Englisch in Wort und Schrift
Sonstiges:
Die Bearbeitung erfolgt in Zusammenarbeit mit einem Industriepartner.