Projektbeschreibung
Übliche Verfahren zur Herstellung von Schaltungsträgern benötigen mehrere Herstellungsschritte, wie beispielsweise beim Kupferkaschieren der Substrate mit anschließendem Subtraktivverfahren zur Strukturierung planarer Leiterplatten. Auch beim “Direct Copper Bonded” (DCB), bei welchem Kupfer mit Aluminiumoxidkeramiken durch einen Brennvorgang stoffschlüssig verbunden werden, folgen mehrere Fertigungsschritte aufeinander, um letztendlich ein strukturiertes Leiterbild zu erhalten. Bei diesen Verfahren jedoch, können die Aspekte der flexiblen Schaltungsträgerherstellung, Materialverbrauch und auch der ökologische Gesichtspunkt nicht hinreichend berücksichtigt werden. Gegensätzlich dazu bietet die Additive Fertigung diesbezüglich eine Lösung. Mittels eines Prozesses können flexible und falls erwünscht 3D-fähige Leiterstrukturen generiert werden. Selbst das keramische Substrat könnte künftig durch SLS (Selektives Lasersintern), je nach Anwendung gefertigt werden. Material wird nur selektiv an bauteilspezifischer Ort und Stelle aufgeschmolzen, was langfristig die Ressourcen schont. Außerdem können dadurch Beschichtungs-, Ätz-, Wasch-, Druck und Metallisierungsvorgänge vermieden werden. Das “Direct to Product”-Alleinstellungsmerkmal der Additiven Fertigung, welches es ermöglicht CAD-Daten direkt nach dem Entwurf zu fertigen, soll anhand dieses Projektes auch in der Produktion leistungselektronischer Elemente für Hochtemperaturanwendungen im Zuge einer Multimaterialverarbeitung eingeführt und angewandt werden.
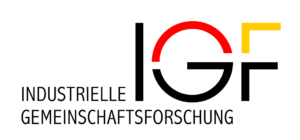
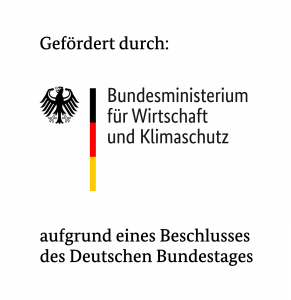