Projektbeschreibung
Durch die stetig steigende Variantenvielfalt, die heutzutage unabdingbar für die Befriedigung der Kundenwünsche ist, muss eine Vielzahl an Teilen an zahlreiche Stationen moderner hochvarianter Fertigungsanlagen geliefert werden. Auf der einen Seite ist eine zuverlässige und flexible Bereitstellung von Teilen unverzichtbar, da andernfalls Materialengpässe zu teuren Bandstillständen führen könnten. Auf der anderen Seite behindern hohe Bestände in Linie-Nähe die Transparenz und die Abläufe in der Fertigung und verringern die für die Wertschöpfung zur Verfügung stehenden teuren Produktionsflächen.
Um unter diesen Rahmenbedingungen kleingranulare produktionssynchrone Materialbereitstellung bei gleichzeitig höchster Versorgungssicherheit im Einklang mit JIT-Prinzipien direkt am Band zu ermöglichen, bietet sich der Einsatz von Pull-Systemen in Verbindung mit einer getakteten Materialversorgung an. Aktuell erfolgt die Materialbereitstellung im Fertigungsbereich aufgrund der Vielzahl an Sachnummern häufig unter Verwendung sogenannter Supermarkt-Konzepte. Diese Supermärkte dienen als dezentralisierte Logistikflächen in Wertschöpfungsnähe, welche Teile für die umliegenden Fertigungs-/ Montagestationen zwischenlagern und gemäß der Bedarfe der Fertigungs-/ Montageprozesse bereithalten. Die Supermärkte wiederum werden durch große Flurförderfahrzeuge oder auch Routenzüge beliefert.
Es muss das Ziel sein, auch bei hoher Variantenvielfalt einen Großteil der Fertigungsfläche für die Wertschöpfung zu nutzen und diese nicht mit Supermärkten, Zwischen- oder Pufferlägern zu belegen. Im Rahmen des Forschungsprojekts „E|SynchroLog“ soll eine Methodik entwickelt werden, welche die Materialversorgung unter Verzicht auf die platz-, energie- und ressourcenverbrauchenden Supermärkte ermöglicht, so dass eine bestandsarme Wertschöpfung auch bei hoher Variantenvielfalt zu geringen Energieverbräuchen und Logistikkosten erfolgen kann. Der innovative Ansatz besteht hierbei darin, die Vorteile der Materialbereitstellung, bspw. durch Routenzüge/ Milkruns, mit den Möglichkeiten intelligenter Sensorik, Industrie-4.0-fähiger PPS-/ERP-/MES-Systeme, eKanban-Lösungen und Routenplanalgorithmik derart zu verknüpfen, dass die Intralogistik ohne die innerbetrieblichen Zwischenlager auskommt und möglichst energieeffizient arbeitet. Dies umfasst überdies zur Optimierung des Gesamtsystems nicht nur die innerbetriebliche Materialversorgung (inbound), sondern auch die externe Supply Chain (outbound).
Das Gesamtziel ist, gleichwohl schwierig zu beziffern, eine Energieeinsparung durch die Systematik (und unter Verwendung weiterer Synergieeffekte) von 20 % im Bereich Intralogistik.
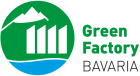