Index
X|CausePro – Expert-Driven Causal Machine Learning in Electronics Production
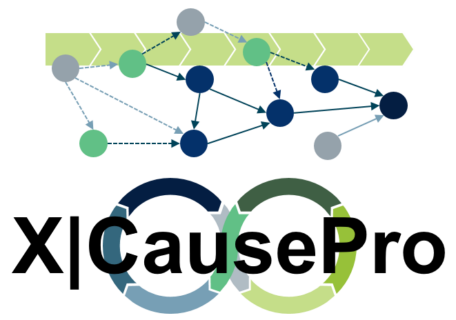
Eine der größten Herausforderungen in der modernen Elektronikproduktion ist die steigende Komplexität von Fertigungsprozessen, insbesondere getrieben durch immer kleinere Dimensionen und zunehmende Funktionalitätsintegration. Zahlreiche Einflussparameter und deren Wechselwirkungen bestimmen die Produktqualität und werden durch konventionelle Methoden immer schwerer beherrschbar. Klassische Machine Learning-Ansätze, die auf reiner Mustererkennung und Korrelation basieren, stoßen hier an ihre Grenzen, wenn es um die Identifikation tatsächlicher Ursache-Wirkungs-Beziehungen geht. Causal Machine Learning (Causal ML) stellt hingegen einen ganzheitlichen Ansatz dar, der es ermöglicht, kausale Zusammenhänge präzise zu quantifizieren und gezielt zu beeinflussen.
Das Verbundvorhaben X|CausePro verfolgt einen innovativen Ansatz zur Überwindung dieser Herausforderungen. Durch die synergetische Kombination von Large Language Models (LLMs), kausalem maschinellen Lernen und einer eventbasierten Dateninfrastruktur sollen nicht nur die Einstiegsbarrieren für kausale Analysen in der Produktion gesenkt, sondern auch nachhaltige Verbesserungen in Produktqualität und Prozesseffizienz erzielt werden.
Im Zentrum des Forschungsvorhabens steht die Entwicklung Methodik, die das Domänenwissen der Elektronikproduktion mithilfe von LLMs automatisiert in Kausalgraphen transformiert. Dieser innovative Ansatz ermöglicht es, verteiltes Expertenwissen aus verschiedenen Quellen zu zentralisieren und formalisieren und durch die Analyse von Produktionsdaten bisher unentdeckte Kausalzusammenhänge zu erschließen. Die Integration in ein speziell für die Fertigung konzipiertes Causal ML-Framework mit Low-Code-Funktionalität und einem intelligenten LLM-Assistenzsystem wird auch Domänenexperten ohne tiefgreifende KI-Kenntnisse den Zugang zu fortschrittlichen kausalen Analysemethoden eröffnen.
Das dreijährige Projekt wird in einem starken Konsortium aus Forschung und Industrie realisiert. Gemeinsam mit den Partnern Ancud IT-Beratung GmbH, PRÜFREX engineering e Motion GmbH & Co. KG und der Schäffler AG sowie den assoziierten Partnern embedded ocean GmbH und Valeo Schalter und Sensoren GmbH arbeiten wir an Lösungen, die Unternehmen helfen, den Paradigmenwechsel hin zu kausal fundierten, datengetriebenen Entscheidungsprozessen in der Produktion erfolgreich zu vollziehen.
CeraClad – Qualifizierung des Laserpulverauftragsschweißen für die schnelle, flexible und direkte Erzeugung leitfähiger Strukturen auf dreidimensionalen Keramiksubstraten
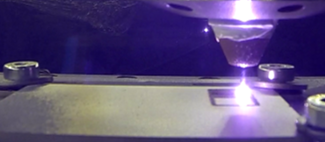
Die fortschreitende Miniaturisierung und die steigenden Anforderungen an Ressourceneffizienz, Leistungsfähigkeit und Variantenvielfalt stellen die Elektronikindustrie vor Herausforderungen. Traditionelle Leiterplattentechnologien stoßen hinsichtlich Materialeinsatz, Prozesskette und Umweltverträglichkeit dabei an ihre Grenzen. Hier kommen Mechatronic Integrated Devices (3D-MID) ins Spiel, die durch räumliche Integration auf Leiterplattenebene kompakte elektronische Systeme mit hoher Funktionsdichte ermöglichen. Die dreidimensionalen, elektrisch isolierenden Grundköper werden im Stand der Technik über Metallisierungsverfahren wie die Laser Direk Strukturierung oder Prozessen der additiven Fertigung mit Leiterbahnen versehen und anschießend mittels Bestück- und Fügeprozesse zu funktionalen Baugruppen aufgebaut. Während die Anforderungen an elektronische Baugruppen zu höhere Strömen und Temperaturen steigen, ist die 3D-MID Technologie aktuell noch auf temperatursensitive Kunststoffe und Verfahren mit geringen Metallisierungsstärken beschränkt. Durch das Projekt CeraClad soll diese Lück durch die Qualifizierung des Laserpulverauftragschweißen (LPAS) für die schnelle, flexible und direkte Erzeugung leitfähiger Strukturen auf dreidimensionalen Keramiksubstraten geschlossen werden.
Im Projekt CeraClad (FKZ 01IF23410N) beforscht der Lehrstuhl FAPS in Kooperation mit dem Laserzentrum Hannover (LZH) und einem aus 14 Unternehmen, davon 8 KMUs, bestehenden projetbegleitenden Ausschuss (PbA) im Rahmen der industriellen Gemeinschaftsförderung (IGF) über 2 Jahre die Metallisierung keramischer Substrate, wobei im ersten Schritt ein zweistufiger Metallisierungsprozess mit niedrigschmelzender Kupfer-Phosphor-Haftvermittlungsschicht und elektrisch funktionalisierender Kupferschicht etabliert werden soll. Aufbauend wird im zweiten Schritt die Bestückung der resultierenden Schaltungsträger mit elektronischen Bauelelementen betrachtet, sodass zum Ende des Projektes ein Technologiedemonstrator resultiert.
LiEp – Laserbearbeitung von Oberflächen in der Elektronikproduktion

Die zunehmende Elektrifizierung der individuellen Mobilität, die Energiewende sowie die Effizienzsteigerung industrieller Prozesse führen zu einem großen Bedarf an leistungselektronischen Wandlern. Diesem Bedarf muss produktionstechnisch mit robusten und automatisierten Fertigungskonzepten begegnet werden, um die Wertschöpfung am Industriestandort Deutschland sichern zu können. Die komplexe und mehrstufige Fertigungskette von Leistungsmodulen erfordert vor allem für hohe Produktionsvolumen funktionale und reproduzierbare Oberflächen, welche in immer kürzeren Entwicklungszyklen flexibel und schnell an neuartige Fügeaufgaben angepasst werden müssen. Die laserbasierte Vorbereitung von technischen Oberflächen in der Elektronikproduktion zeigt hierfür großes Potential auf und soll im Rahmen des Projektes für den industriellen Einsatz entlang der Fertigungskette von leistungselektronischen Modulen erforscht werden.
Ziel des Projektes ist es eine intelligente und bedarfsgerechte Laserbearbeitung zu ermöglichen, welche basierend auf Material-und Prozessmodellen den Sollzustand für anfallende Fügeaufgaben bauteilspezifisch herstellt. Durch den selektiven Charakter örtlich hochauflösender Lasersysteme sollen energie- und kostenintensive Reinigungs- und Vorbehandlungsschritte wie nasschemisches Waschen oder plasmabasierte Kammersysteme innerhalb der Elektronikfertigung substituiert und der CO2-Fußabdruck der Produktion gesenkt werden. Neben fortschrittlichen Belichtungsansätzen zur Realisierung funktionaler Oberflächen soll auch die Beurteilung des Ausgangszustandes hinsichtlich Verunreinigungen, Anomalien und Oberflächeneigenschaften linienintegriert ermöglicht werden. Durch den flexiblen Charakter und die gute Verfügbarkeit von Lasersystemen können so Entwicklungszyklen innerhalb des Produktentstehungsprozesses verkürzt werden, sodass neuartige Lösungen dem Markt schneller bereitgestellt werden können und die Wettbewerbsfähigkeit und Markposition verbessert werden kann. Dies wird vor allem durch die Vielzahl an Kombinationsmöglichkeiten unterschiedlicher Aufbau- und Verbindungskonzepte in elektronischen und leistungselektronischen Baugruppen erforderlich. Über die Realisierung von funktionalen Oberflächen hinaus muss auch die Nutzbarmachung der Oberflächen innerhalb der Prozesskette und Fertigungsumgebung sichergestellt werden, da gemäß dem Stand der Forschung lasergenerierte Effekte durch Alterung teilweise verloren gehen. Hier sollen geeignete Handhabungs- und Montagelösungen erforscht werden, die der Degradation der erzielten Oberflächeneigenschaften innerhalb der Produktionsumgebung entgegenwirken.
Recyclingfähige Vergussmassen für leistungselektronische Module – ECPE Joint Research Programme
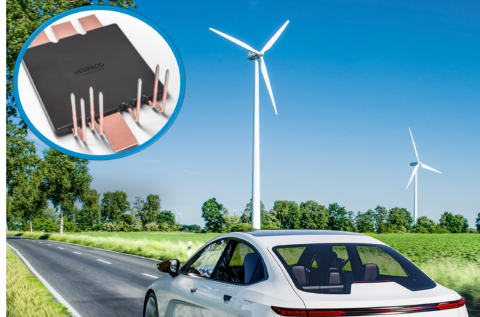
DEEP-Opt – Datenbasierte holistische Energiebedarfsminimierung in der Elektronikproduktion durch Material-, Design- und Prozessoptimierung
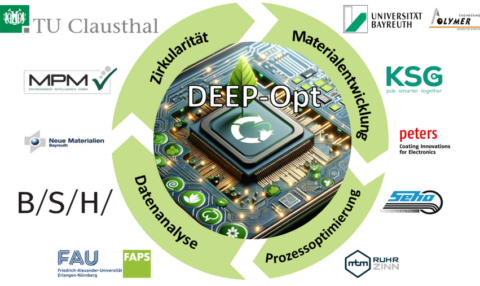
Im Verbundvorhaben DEEP-Opt forscht der Lehrstuhl FAPS gemeinsam mit Partnern aus Wissenschaft und Industrie an der nachhaltigen Elektronikproduktion der Zukunft. Angesichts enormer ökologischer Herausforderungen in der Elektronikbranche, insbesondere hohem Ressourcenverbrauch, gesteigertem Energiebedarf, erheblichen CO2-Emissionen und zunehmendem Elektroschrott, strebt das Projekt DEEP-Opt eine umfassende Verbesserung von Nachhaltigkeit und Ressourceneffizienz in der Elektronikproduktion an. Das Konsortium forscht entlang der gesamten Wertschöpfungskette an unterschiedlichen Ansätzen, um den Ressourcen- und Energiebedarf sowie die CO2-Emissionen in der Elektronikproduktion deutlich zu reduzieren.
Im Fokus stehen die Entwicklung umweltfreundlicherer Leiterplattensubstrate, einschließlich recyclingfähiger und biobasierter Werkstoffe als Alternativen zu den herkömmlichen FR4-Materialien, sowie die Anpassung der Fertigungstechniken und -prozesse an diese neuen Materialsysteme. Zusätzlich wird die Energieeffizienz bestehender Fertigungsprozesse optimiert. Beispiele hierfür sind die Entwicklung eines energieeffizienten, mittels Inkjet-Verfahren applizierbaren Lötstopplacks und die Forschung zu niedrigschmelzenden Loten für die Flachbaugruppenmontage. Umfangreiche Qualitätsprüfungen der Flachbaugruppen stellen sicher, dass Verbesserungen in Ressourcen- und Energieeffizienz nicht zu Lasten der Produktqualität und -zuverlässigkeit gehen.
Ein weiteres Schlüsselelement ist die Förderung der Zirkularität, um nachhaltige und geschlossene Materialkreisläufe in der Elektronikfertigung zu etablieren. Das Circular Design-Konzept, das eine leichte Demontage am Ende des Produktlebenszyklus und die effiziente Wiederverwendung oder das Recycling der Materialien vorsieht, minimiert den Ressourcenverbrauch und reduziert Elektroschrott. Die Integration dieser zirkulären Designprinzipien unterstützt den Übergang zu einer Kreislaufwirtschaft und die Entwicklung neuer Recyclingmethoden für traditionelle und alternative Materialsysteme. Zusätzlich wird an innovativen chemischen Recyclingverfahren für Leiterplattensubstratmaterialien geforscht, um die Nachhaltigkeit in der Branche weiter voranzutreiben.
Parallel dazu erfolgt die kontinuierliche Erfassung von Primärenergiedaten und Prozesszeiten, die eine transparente und objektive Bilanzierung alternativer Wertschöpfungsketten ermöglicht. Umfassende Lebenszyklusanalysen dienen der ganzheitlichen Bewertung der Primärenergiebedarfe und fließen in die Optimierung der Wertschöpfungsketten ein. Das Konsortium verfolgt das ambitionierte Ziel, den Primärenergieverbrauch und die CO2-Emissionen im Vergleich zum Benchmark-System FR4 um mindestens 40 % zu reduzieren, was wesentlich zur Entwicklung einer ressourcenschonenden Elektronikindustrie beiträgt.
Die Verwertungsstrategie des Projekts zielt darauf ab, die Forschungsergebnisse einem breiten Publikum zugänglich zu machen und maximale Wirkung zu erzielen. Ein wichtiger Aspekt ist die Überführung der Ergebnisse in mindestens ein Demonstrationsszenario, um den Wissenstransfer zu stärken und die Akzeptanz sowie Implementierung neuer, nachhaltiger Wertschöpfungsketten in der Elektronikindustrie zu fördern. Ein Leitfaden mit detaillierten Anleitungen und Best Practices zur Nutzung nachhaltiger Materialien und zur Optimierung der Energieeffizienz in der Flachbaugruppenfertigung wird bereitgestellt, um die Ergebnisse und Erkenntnisse aus dem Projekt direkt in die industrielle Praxis zu übertragen und eine breite Anwendung sowie Akzeptanz der entwickelten nachhaltigen Ansätze und Technologien zu fördern.
IntelRadar – Intelligentes Radarsystem durch Kombination von additiver Fertigung, hardware-integrierter Rechnerarchitektur und smarten Prüfroutinen
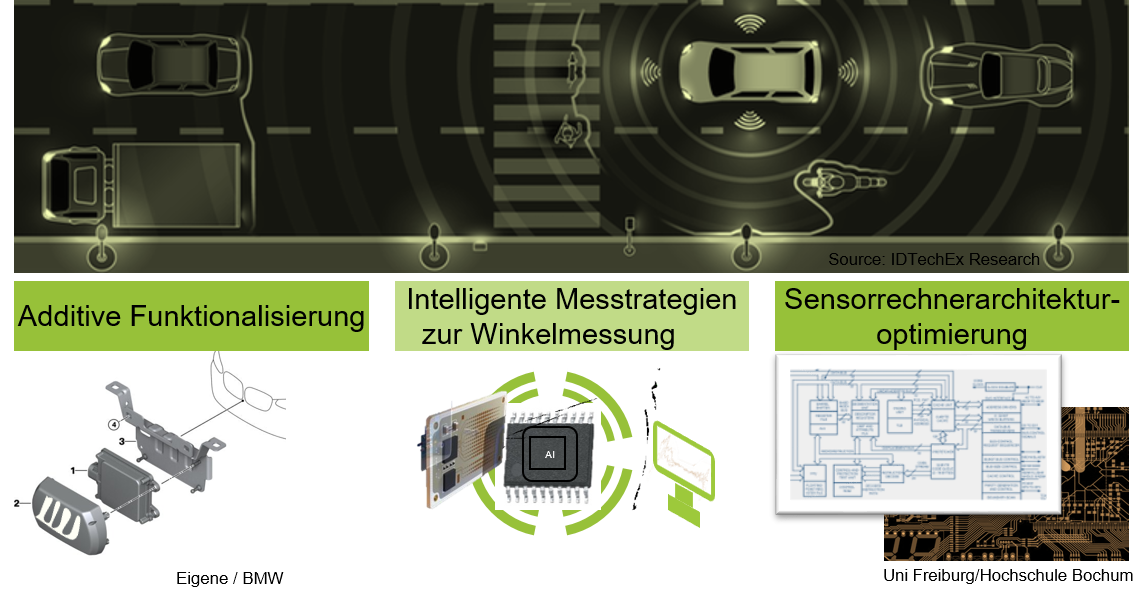
Der Wunsch nach hochautomatisiertem Fahren erfordert intelligente und vernetzte Fahrzeuge, welche mittels präziser Sensorik ihre Umgebung detailliert und zuverlässig erfassen können. Neben Kameras, Ultraschall- und Lidarsensoren sind Radarsensoren von großer Bedeutung im Automobil der Zukunft. Höchste Genauigkeit und Zuverlässigkeit, z.B. für die Radar basierte Umfelderkennung auf weite Entfernungen von über 200 m, ist essentiell. Diese wird maßgeblich beeinflusst durch die Signalstreuung- und Dämpfung, Antennengüte und Auswerteelektronik, sowie Algorithmen. Aufgrund dieser Einflüsse müssen als wesentliche Voraussetzung für präzise Erfassung Antenne, (Sekundär-)Radom (Sensorabdeckung) und Auswerteelektronik perfekt aufeinander abgestimmt und als Gesamtsystem integriert sein. Dies schließt, um Test- und Auswertezeiten zu minimieren, auch neue Ansätze für die Funktionsprüfung durch den Einsatz Künstlicher Intelligenz für die Sensoralgorithmik und Sensortests mit ein.
Ziel des Projekts ist die Verbesserung eines automobilen Radarsystems entlang der Fertigungskette von der Elektronikarchitektur des Sensors, der Entwicklung einer KI-gestützten Prüfroutinenoptimierung der Winkelkalibration des Sensors und der Integration von resistiven Radomheizelementen mittels additiver Funktionalisierung auf Freiformgehäusen. Hierdurch soll die Zuverlässigkeit des Radarsystems erhöht werden. Dabei wird ein ganzheitlicher Ansatz verfolgt, der in Form eines Demonstratorsystems am Ende des Projekts validiert werden soll.
Projektziele
- Verbesserung automobiler Radarsysteme
- Ganzheitliche Betrachtung der Fertigungskette
- Optimierung der Hardwarearchitektur des Radars
- Sensor-Prüfzeitreduzierung durch KI-Algorithmen
- Integration resistiver Heizelementen mittels gedruckter Elektronik auf 3D-Geometrien
Prozesse zur additiven Fertigung von 3D-Schaltungsträgern: Ableitung von Designregeln aus Zuverlässigkeitsuntersuchungen
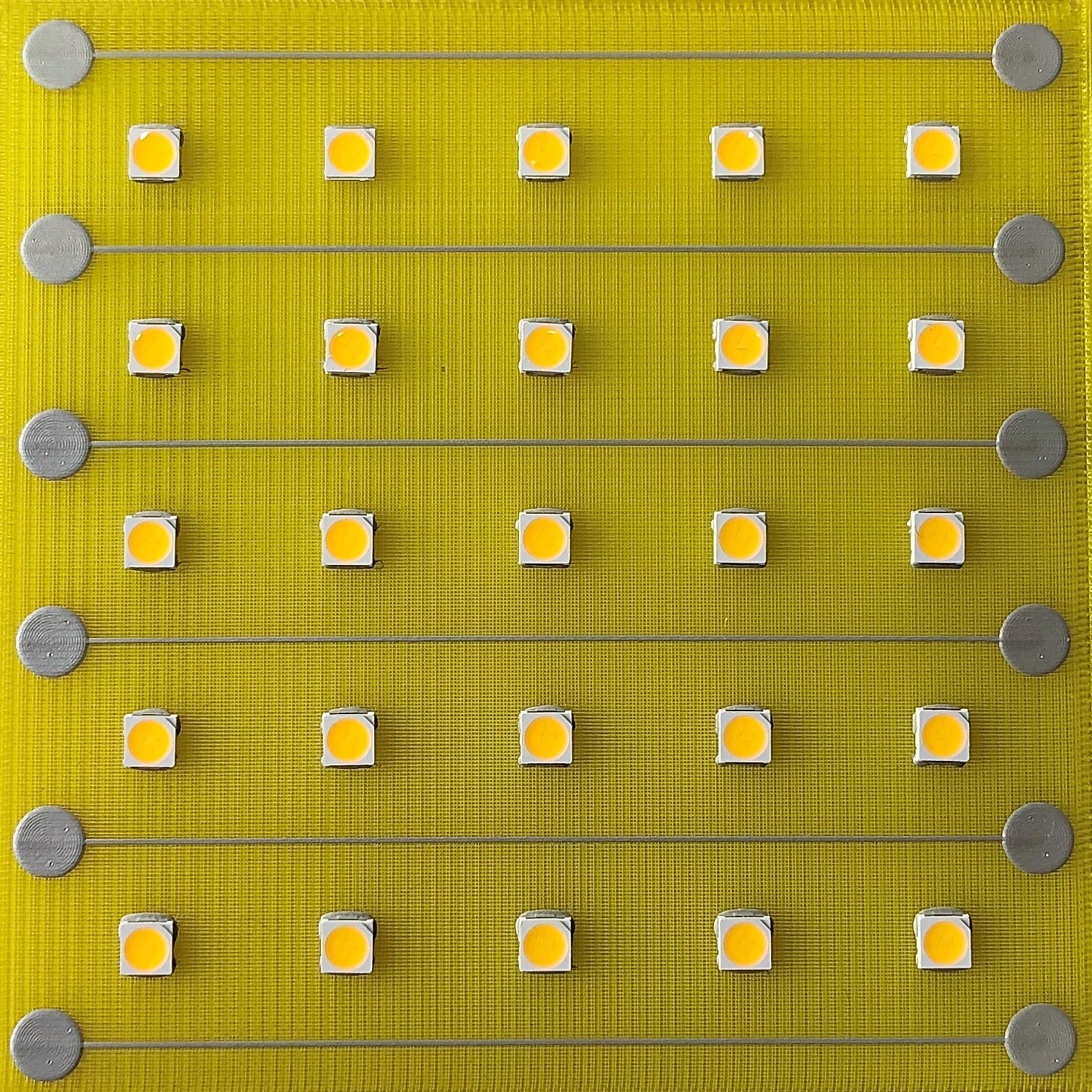
Das heutige Produktionsumfeld ist unter anderem geprägt von den Megatrends Kundenindividualisierung, Konnektivität und Digitalisierung. Aus diesen ergibt sich unter anderem die Notwendigkeit, mechanische Bauteile mit integrierter Intelligenz in kleinen Stückzahlen wirtschaftlich herstellen zu können. Gleichzeitig soll die Integration der zusätzlichen Funktionen nicht dem Streben nach Miniaturisierung entgegenwirken. Zudem wird aus ökonomischen und ökologischen Überlegungen heraus eine energie- und ressourcenschonende Produktion angestrebt. Trotz über 15 Jahren weltweiter Forschung an Prozessketten, insbesondere der additiven Fertigung, besteht die Notwendigkeit, den Reifegrad der Prototypenfertigung zu überwinden und die Langzeitbeständigkeit der hergestellten Bauteile nachzuweisen.
Im Projekt Pistazie sollen Prozessketten für die additive Herstellung von mechatronischen Prüfkörpern ausgewählt und eingesetzt, die aufgebauten Prüfkörper verschiedenen Belastungstests unterzogen und Daten zu Ausfallzeitpunkt und Ausfallursache erhoben werden. Die Grundkörper werden dabei mit additiven Fertigungsverfahren wie dem Fused Filament Fabrication (FFF), Digital Light Processing (DLP), Material Jetting (MJT), Selective Laser Sintering (SLS) und anderen Verfahren hergestellt. Anschließend werden die Bauteile mit den Verfahren LDS, Inkjet und Aerosol-Jet funktionalisiert. Die Haftfestigkeit der leitfähigen Schichten auf dem Substrat sowie die Lötbarkeit auf den Metallstrukturen wird untersucht, um ungeeignete Prozessketten erkennen zu können.
Die Prüfverfahren orientieren sich an den Hauptausfallursachen für elektronische Bauteile, also Temperaturwechsel, Vibrationen und Feuchte, und werden durch eine statistische Versuchsplanung unterstützt. Auf der Grundlage der ermittelten Daten sollen allgemeine Designregeln abgeleitet werden, die es Unternehmen prozessspezifisch ermöglichen, langlebige Produkte zu entwerfen und dadurch dazu führen, die über Jahre erforschten Prozessketten in der Industrie zu etablieren.
ColEP – Kollaborative Nutzung von Daten in der Elektronikproduktion
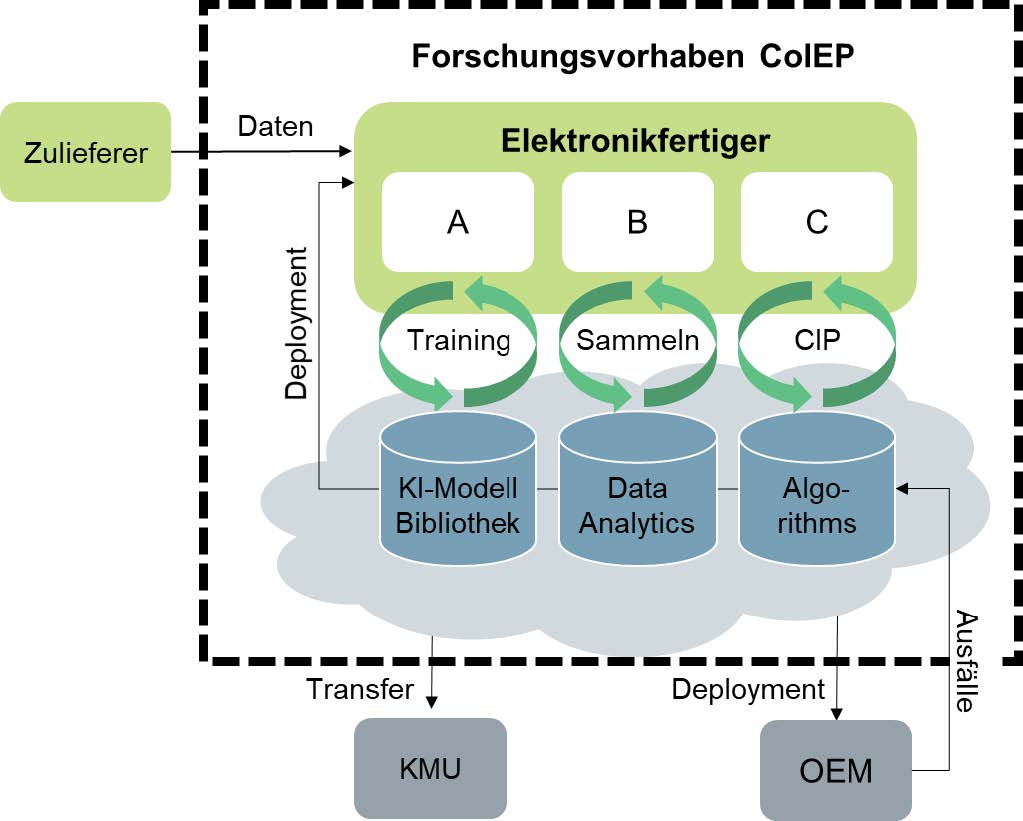
Eine zentrale Herausforderung für den Einsatz datenbasierter Methoden zur Analyse und Optimierung von Prozessen in der Elektronikproduktion besteht in der Unausgeglichenheit der Daten. Trotz der großen anfallenden Datenmengen in Hochvolumenproduktionen ist der Informationsgehalt der Daten begrenzt, da bei der überwiegenden Mehrheit der Inspektionen keine Fehler erkannt werden. Um einen Fehlerschlupf zu vermeiden sind die automatisierten Inspektionsschritte, welche in der Regel auf konventionellen Bildverarbeitungsmethoden basieren, so sensitiv eingestellt, dass meist eine relativ hohe Rate an Pseudofehlern entsteht. Diese Bauteile erfüllen eigentlich die Spezifikationen, werden jedoch fälschlicherweise als fehlerhaft eingestuft, sodass ein hoher manueller Nachprüfaufwand entsteht.
Um diesen Aufwand zu reduzieren können als fehlerhaft identifizierte Bauteile mittels KI-Methoden nachgeprüft werden, sodass ein Teil der Pseudofehler erkannt wird, was eine Reduktion des Prüfaufwands zur Folge hat. Die Qualität der eingesetzten KI-Methoden ist entscheidend von der verfügbaren Datenmenge und -qualität abhängig. Um trotz der unausgeglichenen Datenlage in der Elektronikproduktion eine große Datenbasis zu Verfügung zu haben, werden im Forschungsvorhaben ColEP Vorteile und informationstechnische Lösungen der kollaborativen Verwertung von Prozess-, Qualitäts- und Metadaten von Elektronikfertigern und Anlagenherstellern untersucht. Dabei werden anhand ausgewählter KI-Anwendungsfälle in der Elektronikproduktion Verbesserungspotentiale analysiert, für die kollaborative Datensätze besonders geeignet erscheinen. Diesbezüglich erfolgt eine automatisierte Anonymisierung und Aufbereitung der Daten, um eine Grundsicherheit zu gewährleisten. Weiterhin wird unter Nutzung der GAIA-X-Konzepte ein Framework erarbeitet, dass die Souveränität der Daten für den Besitzer sicherstellen soll.
In diesem Kontext werden sowohl Frameworks zum föderalen Lernen als auch die Einbindung in existierende souveräne Dateninfrastrukturen untersucht. Im Gegensatz zu zentralisiertem Lernen, bei welchem Daten aus unterschiedlichen Quellen auf einem zentralen Server gesammelt werden, bleiben beim föderalen Lernen Trainingsdaten jederzeit lokal bei den teilnehmenden Unternehmen, wodurch Datensicherheit und -souveränität gewährleistet sind. Das Modelltraining erfolgt lokal, woraufhin die trainierten Modelle zu einem zentralen Server gesendet werden, welcher diese zu einem globalen Modell vereint.
Ziel des Projekts ist es, die Anwendbarkeit von föderalem Lernen im industriellen Kontext anhand von Use Cases in der Elektronikproduktion zu untersuchen. Dabei soll sowohl ein Vergleich der Modellperformance beim föderalen Lernen mit zentralisiertem und lokalem Lernen stattfinden. Zudem sollen datenschutzspezifische Vorteile von föderalem Lernen untersucht und sicherheitsrelevante Herausforderungen wie Datenmanipulation und Rekonstruktion von Trainingsdaten kritisch betrachtet und durch geeignete Methoden verhindert werden.
NiMm3 – Nickelfreie Metallisierungssysteme auf 3D MID Substratwerkstoffen
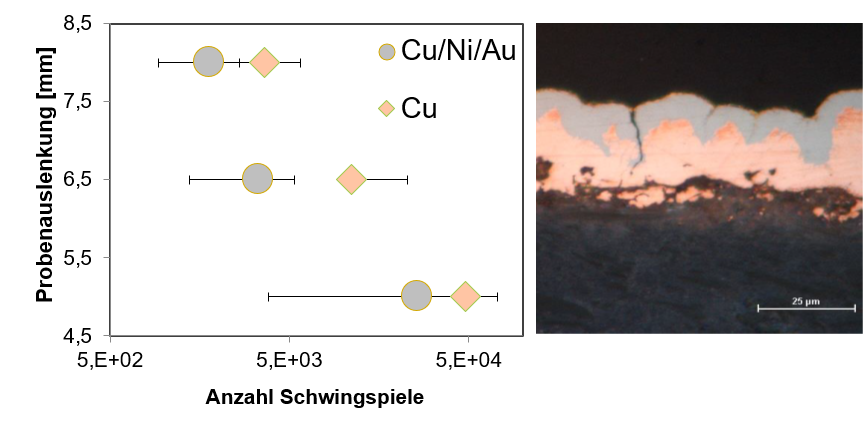
Molded Interconnect Devices (MIDs) sind meist thermoplastische 3D-Substratmaterialien, die typischerweise zunächst Laserdirektstrukturiert (LDS) und danach außenstromlos mit Kupfer, Nickel und Gold metallisiert werden. Dabei fungiert das direkt auf dem Substrat befindliche Kupfer als elektrischer Leiter, während die Nickelschicht die Diffusionsbarriere zur Goldoberfläche darstellt. Letztere ermöglicht verschiedene Aufbau- und Verbindungstechniken (AVT) für elektronische Komponenten wie z.B. Löten, leitfähiges Kleben und Drahtbonden, um schließlich komplexe Schaltungsträger mit einer hohen Integrationsdichte zu erhalten.
Die Zuverlässigkeit der metallischen Leiterbahnen auf LDS-fähigen Substratwerkstoffen ist eine wesentliche Grundvoraussetzung für die brachenübergreifende Anwendung von MIDs. Eine Befragung von Vertretern aus der Industrie zum Thema Zuverlässigkeit von MIDs ergab, dass Delamination sowie die Entstehung von Mikrorissen in den Leiterbahnen die häufigsten Ausfallursachen von MIDs darstellen. Daher ist das Bestreben groß diese beiden Ursachen weitmöglichst zu unterbinden, um so die Zuverlässigkeit und Lebensdauer von MIDs deutlich zu steigern und deren Marktdurchdringung weiter voranzutreiben.
Herausforderung
Ausfallursache 1: Delamination
Die Wahl des Substratmaterials und der verwendete Laserparametersatz beeinflussen maßgeblich sowohl die Haftfestigkeit zwischen Substrat und Kupfer als auch die Differenz deren thermischer Ausdehnungskoeffizienten. Letzteres ist nicht nur für die Anwendung von MIDs bei erhöhten Temperaturen relevant, sondern spielt auch für die AVT, z.B. beim Löten, eine wesentliche Rolle.
Ausfallursache 2: Mikrorisse
Studien im Rahmen der IGF Vorhaben LDS-MID-ChaMP (16737N) und MetaZu (19754N) haben gezeigt, dass Leiterbahnrisse überwiegend in der Nickelschicht entstehen. Diese Mikrorisse weiten sich durch weitere Belastung aus und dringen in die Kupferschicht vor. Bei zu großer Belastung führen diese schließlich zum Ausfall der Leiterbahn und damit zum Versagen des Schaltungsträgers.
Lösungsansatz
Um die beiden genannten Ausfallursachen zu eliminieren werden im geplanten IGF Vorhaben NiMm3 drei aufeinander aufbauende Themen adressiert.
1. Wechselwirkung zwischen Substratmaterial und Kupfermetallisierung
Es werden verschiedene Substratmaterialien betrachtet. Zusätzlich zu Thermoplasten kommen Duroplaste und Keramiken für einen erweiterten Einsatzbereich von 3DSchaltungsträgern infrage. Durch Variation der Laserparametersätze wird Einfluss auf Rauheit und Haftfestigkeit, und dadurch auf die Zuverlässigkeit der Leiterbahn unter mechanischer und thermischer Belastung (Biegewechselfestigkeitstests und Umwelttests) genommen. Bildgebende Verfahren wie die Ultraschall-Mikroskopie (SAM) und die Untersuchung von Querschliffen mittels Rasterelektronenmikroskopie können weitere wichtige Erkenntnisse liefern.
2. Alternative, nickelfreie Schichtsysteme
Es werden verschiedene nickelfreie Schichtsysteme untersucht und mit dem etablierten Schichtsystem Cu/Ni/Au verglichen. Mögliche Varianten sind hierbei Cu/Ag, Cu/Sn, Cu/Pd/Au, Cu/Au sowie Cu/OSP (org. Passivierung). Auch hier werden Leiterbahnen u.a. unter mechanischer und thermischer Belastung betrachtet. Wobei nicht nur das Schichtsystem variiert wird, sondern auch die Schichtdicke der einzelnen Komponenten.
3. AVT und Einfluss des Lötprozesses
Die Bestückung mit elektronischen Komponenten ist in der MID Technologie ein wesentlicher Schritt hin zu hochintegrierten Schaltungsträgern. Daher wird abschließend die Korrosionsbeständigkeit und Lötbarkeit bzw. Bondbarkeit der verschiedenen Oberflächen-Finishes betrachtet, sowie der Einfluss des Lötprozesses auf die Haftfestigkeit der Metallisierung z.B. mittels Schertests und SAM untersucht.
Additive Herstellung von Metall-Keramik-Verbunden mittels selektivem Laserschmelzen
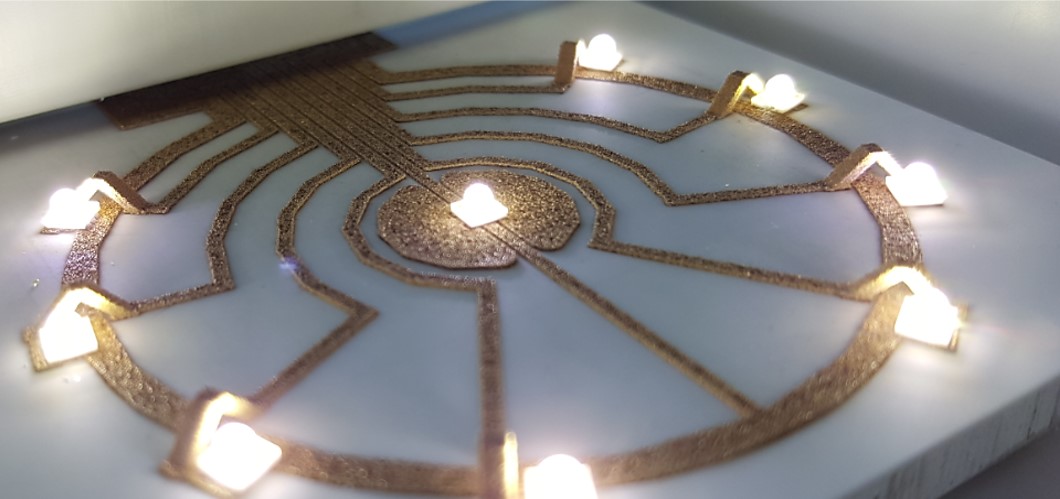
Vorliegendes Vorhaben beschäftigt sich mit der Erforschung der additiven Herstellung von Metall-Keramik-Verbunden mittels selektivem Laserschmelzen für die Leistungselektronik. Als leistungselektronische Substratmaterialien werden derzeitig meist keramische Schaltungsträger, gefertigt anhand von DCB- (direct copper bonded) oder AMB- (active metal brazing) Verfahren, angewandt. Beide Verfahren beinhalten den Verbund von keramischem Substrat mit einer metallischen, elektrisch leitenden dünnen (0,2-0,5 mm) Schicht, meist in Form von Folien. Die Verbindung der beiden Werkstoffe wird beim DCB-Prozess über die Benetzung von geschmolzenem Cu2O an der Kupferfolienunterseite in direktem Kontakt mit einer Oxidkeramik (meist Al2O3) in einem Brennprozess bei ca. 1064 °C erzielt. Dadurch wird eine stoffschlüssige Verbindung erzielt, welche im Einsatz von leistungselektronischen Schaltungsträgern aufgrund der CTE-Unterschiede von Keramik und Metallisierung notwendig ist. Beim AMB-Prozess sind es Titanzusätze zu einer Lotlegierung (meist Ag-Cu-Lote), welche beim Brennprozess in Kontakt mit keramischen Materialien eine Reaktionsschicht ausbilden. Besagtes Lot fungiert demnach als Interface zwischen keramischem Substrat und Metallfolie. Beide Prozesse weisen jedoch Schwächen im Bereich der Flexibilisierung, 3D-Fähigkeit der Metallisierung und dem Ressourcenverbrauch auf. Um letztlich die leitenden Strukturen des Schaltungsträgers zu erhalten sind diverse Lithographie-, Ätz-, und Waschvorgänge nötig, welche die Prozesskette maßgeblich verlängern und zusätzlich die Umwelt durch den Einsatz von Chemikalien belasten.
Das selektive Laserschmelzen bietet hierfür eine Alternative: Es können Pulvermaterialien auf ca. 500 °C heißen keramischen Substraten in einem Prozessschritt selektiv geschmolzen werden, was der letztendlichen Metallisierung entspricht. Dieses Verfahren kann als selektives Laser Brazing (SLB) beschrieben werden. In diesem Forschungsvorhaben werden aufgrund der Analyse des Standes der Technik und den umfangreich durchgeführten Vorarbeiten Cu-Ti-Pulver als Metallisierungsmaterialien verwendet. Als Substratmaterial soll Al2O3 fungieren. Zu Beginn des Forschungsvorhabens wird das Schmelzverhalten der Pulvermaterialien ohne keramischem Substratmaterial qualifiziert. Hauptbestandteil der Forschung jedoch ist die Ermittlung des Benetzungsverhaltens der Pulver auf der beheizten Al2O3-Keramik mit einhergehenden Parameterstudien. Als Qualifizierungsmaßnahmen werden Haftfestigkeitsprüfungen, Stromtragfähigkeiten sowie Langzeitstabilitäten der Metallisierung vor und nach einer thermischen Nachbehandlung in inerter/evakuierter Atmosphäre überprüft. Anhand von EDX- und WDX-Analysen im REM soll die Kernfragestellung – der Möglichkeit einer stoffschlüssigen Verbindung von Titanhaltigen Pulver mit Al2O3 in Form von einer Ausbildung von Magneli-Phasen mittels SLB/SLM – des Forschungsvorhabens beantwortet werden.