Index
EMGRoll – Intuitive Steuerung von Rollstühlen mittels hochaufgelöster Muskelsignale
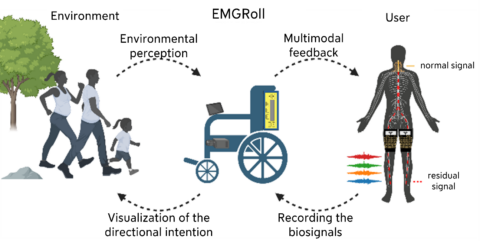
Mobilitätseinschränkungen haben weitreichende Folgen für den Alltag der Betroffenen und führen neben der körperlichen Einschränkung häufig auch zu psychischen Problemen. Der Rollstuhl stellt für die Betroffenen die einzige Möglichkeit dar, am täglichen Leben teilzunehmen. Aufgrund von Funktionseinschränkungen der oberen Extremitäten, beispielsweise durch eine Querschnittlähmung, können jedoch nicht alle Menschen mit Behinderung einen klassischen Rollstuhl bedienen. Auch die Bedienung eines elektrisch angetriebenen Rollstuhls ist davon betroffen. Neben körperlichen Einschränkungen können auch unzureichende motorische oder kognitive Fähigkeiten ein Hindernis für die selbstständige Nutzung eines Rollstuhls darstellen und damit die Teilhabe am täglichen Leben einschränken.
Ziel von EMGRoll ist die Erforschung eines Sensorkits, das durch die Kombination von EMG-Signalen und Sensoren zur Umgebungserfassung eine intuitive und assistierte Steuerung von elektrisch angetriebenen Rollstühlen ermöglicht. Basierend auf der Erkenntnis, dass bei den meisten querschnittgelähmten Patienten noch eine neuronale Verbindung zwischen Gehirn und Muskeln besteht, hat das n-squared lab unter Leitung von Prof. Dr. Alessandro Del Vecchio ein Brain-Machine-Interface entwickelt. Dieses soll in EMGRoll auf die unteren Extremitäten erweitert werden, um die Bewegungsintention der Beine zu messen und an die Steuerung des Rollstuhls weiterzugeben. Um die Bewegungsintention intelligent an die Umgebung anzupassen, soll die vom Lehrstuhl für Fertigungsautomatisierung und Produktionssystematik (FAPS) unter Leitung von Prof. Dr. Jörg Franke entwickelte autonome Navigation für Rollstühle genutzt werden, um eine geteilte Steuerung des Rollstuhls zwischen Nutzer und intelligenter Maschine zu erforschen.
PreciEye – Präzisierung der berührungslosen Augeninnendruckmessung zur Selbstdiagnostik
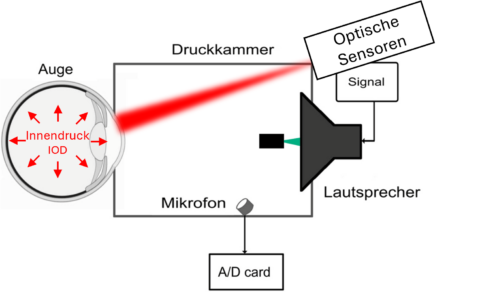
Glaukome sind weltweit eine der häufigsten Ursachen für Erblindungen und betreffen insbesondere ältere Menschen. In Deutschland erkranken etwa 2-4 % der über 65-Jährigen an dieser Krankheit, was jährlich zu 1.000 Neuerblindungen führt.
Das Glaukom entsteht durch eine Degeneration der neuronalen Ganglienzellen im Sehnerv, häufig infolge eines erhöhten Augeninnendrucks (IOD). Dieser erhöhte Druck ist ein wesentlicher Risikofaktor, und seine Senkung bleibt die einzige Behandlungsoption. Die frühzeitige Erkennung und Behandlung dieser Degeneration ist essentiell, da der bisherige Verlust der Sehfähigkeit nicht rückgängig gemacht werden kann. Für eine optimale Diagnose und Therapieplanung ist die Erfassung einer Tagesdruckkurve notwendig, da diese über den Tagesverlauf stark schwankt.
Um eine augenschonende und selbstständige Messung zu ermöglichen, wurde am BIMAQ ein Konzept erarbeitet, bei dem der IOD kontaktlos aus der Schwingungscharakteristik des Auges bestimmt wird. Da die Messung indirekt erfolgt und von der Handhabung des Geräts abhängig ist, sollen die Ergebnisse im Projekt PreciEye über zusätzliche Sensorik und durch maschinelles Lernen abgesichert werden.
GraspAgain – Wiederherstellung der Handfunktion bei neuromuskulären Einschränkungen durch eine intelligente Neuroorthese
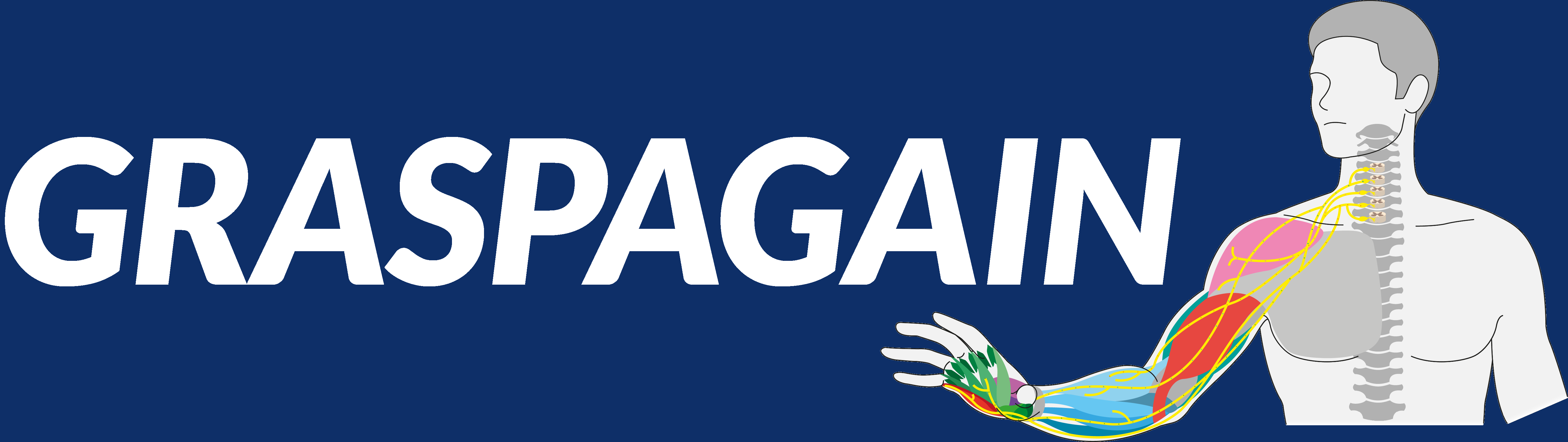
Weltweit leiden 50 Millionen Menschen unter neuromotorischen Beeinträchtigungen der Hand aufgrund einer Rückenmarksverletzung oder eines Schlaganfalls. Infolgedessen sind diese Menschen in den Aktivitäten des täglichen Lebens enorm eingeschränkt. Es wurde bereits gezeigt, dass Neuroorthesen die Hände gesunder Menschen bewegen können. Allerdings gibt es noch Forschungs- und Entwicklungsbedarf, um einzelne Finger einer gelähmten Hand zu bewegen. Das Projekt GraspAgain zielt mit einer intelligenten Neuroorthese darauf ab, die Handfunktion von Menschen mit neuromuskulären Einschränkungen wiederherzustellen. Das Projekt umfasst zwei Forschungsschwerpunkte: ein nichtinvasives Brain-Machine-Interface und eine Mechatronik. Ein interdisziplinäres Projektteam mit hoher Fachexpertise kann bereits auf gemeinsame Vorarbeiten zurückgreifen. Wir sind der Überzeugung, mit GraspAgain ein revolutionäres Produkt erschaffen zu können, das Menschen mit Handbeeinträchtigungen wieder ein unabhängigeres Leben ermöglichen soll.
Kicks4Edge
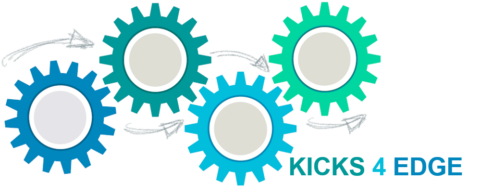
Das Forschungsprojekt „Kicks4Edge“ zielt darauf ab KMU dazu zu befähigen ihre Produktion und Prozesse mithilfe von Cloud-Edge-Technologien zu digitalisieren. Hierfür fördert das Projekt die Interoperabilität von heterogenen Produktions- und Steuerungssystemen sowohl durch Konnektivität und Schnittstellen als auch durch neue Software- und Serviceangebote für offene industrielle Edge-Systeme und digitale Geschäftsmodelle. Außerdem soll ein offenes „Industrial Edge Ökosystem“ gefördert und gepflegt werden.
Produzierende Unternehmen können sich für ein Starter Paket (Industrial Edge Test Kit) bewerben und bekommen im Rahmen von Workshops den Umgang mit dem Starter Paket beigebracht. Anschließend können die Unternehmen mit einem Starter Paket verschiedene Edge-Anwendungsfälle bei sich ausprobieren und valideren.
Im Anschluss an diese Testphase führt der Lehrstuhl FAPS in Kooperation mit dem Lehrstuhl Wi1 qualitative Interviews mit den Unternehmen durch. Basierend auf diesen Interviews wird im Zuge des Projekts ein „Edge Playbook“ erstellt, welches als Leitfaden zum Einsatz von Edge Devices in verschiedenen Anwendungsszenarien dienen soll, um Anwender bei der Identifikation, Entwicklung und Umsetzung ihrer eigenen Use Cases zu unterstützt.
TEKTONIK: Tektonische Veränderung der Wertschöpfung durch digitale Plattformen: Neue Impulse für Kollaboration, Transparenz und Optimierung in vernetzten Wertschöpfungssystemen
Das Ziel von TEKTONIK besteht in der umfassenden Betrachtung digitaler Plattformen im Kontext des produzierenden Gewerbes. Insbesondere werden die industrielle Anwendung, Klassifizierung und Systematisierung, Industriestandorte und regionale Kompetenzcluster sowie rechtliche und politische Rahmenbedingungen eingehend untersucht. Der gewählte System-Dynamics-Ansatz ermöglicht die Modellierung, Simulation, Analyse und Gestaltung dynamisch-komplexer Prozesse, Rollen, Informationen sowie des Produktions- und Liefernetzwerks.
Zur Erreichung des Ziels werden die oben genannten Themenfelder im Hinblick auf ihre Priorisierung sowie Fokussierung unterteilt. Die „Industrielle Anwendung“ sowie „Klassifizierung und Systematisierung“ werden den primären Themenbereichen zugeordnet, welche im Einklang mit den aktuellen Forschungsschwerpunkten des FAPS liegen. Sekundäre Bereiche, zu denen die Themen „Industriestandorte und regionale Kompetenzcluster“ sowie „Rechtliche und politische Rahmenbedingungen“ werden jedoch mitbetrachtet, um der gesamtheitlichen, interdisziplinären Komplexität digitaler Plattformen gerecht zu werden.
Themenfeld 1: Industrielle Integration und Anwendung
Das Themenfeld Industrielle Integration und Anwendung befasst sich unter Nutzung analytischer und wissenschaftlicher Methoden mit dem Status Quo sowie den zukünftigen Perspektiven industriellen Plattformen im produktionstechnischen Umfeld. Dabei dient die Produktion mechatronischer Systeme als praxisbezogenes Anwendungsfeld.
Themenfeld 2: Systematisierung und Klassifizierung
Das Themenfeld Systematisierung und Klassifizierung erforscht die interne sowie externe Dynamik industrieller Plattformen. Ziel ist die Untersuchung und methodische Einordnung komplexer Rollenverständnisse, Governance, Organisationsformen sowie Schnittstellen auf und zwischen Plattformen, um diese in einer allgemeingültigen Referenzstruktur aufgehen zu lassen.
Themenfeld 3: Industriestandorte und regionale Kompetenzcluster
Das Themenfeld „Industriestandorte und regionale Kompetenzcluster“ umfasst die Untersuchung lokaler Einflussfaktoren auf industrielle Plattformen. Darauf aufbauend wird der Einfluss von industriellen Plattformen auf Standortfaktoren abgeleitet. Im Fokus liegen die Standortstrategie industrieller Unternehmen sowie die perspektivische Clusterbildung durch industrielle Plattformen im Sinne der europäischen Clusterpolitik.
Themenfeld 4: Rechtliche und politische Rahmenbedingungen
Das Themenfeld der juristischen und politischen Rahmenbedingungen zielt auf die durchgehende Überprüfung und Harmonisierung der Ergebnisse mit geltenden gesetzlichen Vorgaben und Entwicklungen ab. Dabei wird nicht nur die juristische Umsetzbarkeit der gewonnen Ergebnisse betrachtet, sondern auch Handlungsempfehlungen für eine Anpassung der gesetzlichen und politischen Rahmenbedingungen geäußert.
Über Impuls- und Diskussionspapiere sowie wissenschaftliche Publikationen werden die Ergebnisse schnell einer breiten Öffentlichkeit zugänglich gemacht. Kurz- und mittelfristig soll der Wissenstransfer in die Wirtschaft, vor allem an KMU, gesichert werden. Somit können die Ergebnisse dazu beitragen, die volkswirtschaftliche Bedeutung von industriellen Plattformen hervorzuheben und Unternehmen die wertschöpfende Nutzung von diesen zu ermöglichen.
AKKI-KS – Einsatz von künstlicher Intelligenz zur Reduzierung des Energieverbrauchs und der CO2-Emissionen bei der Autoklavierung von Kalksandsteinen
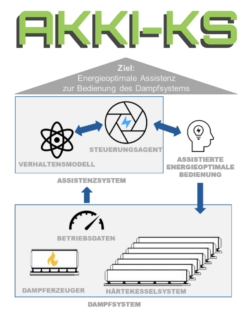
Die Umsetzung der Kalksandstein-Roadmap erfordert u.a. Maßnahmen im Bereich der Digitalisierung. Hier ist eine Reduzierung des Energieverbrauchs und der CO2-Emissionen durch optimalen Betrieb von Autoklavensystemen möglich. Herzstück des Autoklavierungsprozesses ist in jedem KS-Werk das Dampfsystem. In den meisten KS-Werken sind Anlagentechnik und Steuerung prinzipiell ähnlich aufgebaut. Durch unterschiedliche Anlagendetails und Prozessspezifika ergibt sich jedoch ein anlagenspezifisches Verhalten des Dampfsystems. Aufgrund der hohen Prozesskomplexität und Systemdynamik – insbesondere bei Überleitvorgängen – ist eine vollständig algorithmische Modellierung nur mit hohem experimentellem Aufwand zu erreichen. In der Folge können die korrekten Betriebsparameter für die Anlagen nur aus Erfahrungswerten geschätzt werden. Häufig wird leider zugunsten des Durchsatzes auf Energieeffizienz verzichtet. Mit diesem Forschungsprojekt soll deshalb durch den Einsatz von künstlicher Intelligenz eine aufwandsärmere Methodik erforscht werden, wie ein energieoptimaler Betrieb von Autoklavensystemen erreicht werden kann. Dafür soll eine KI-Software aus vorliegenden Produktionsdaten das werksspezifische Verhalten der Dampfsysteme erlernen. Ein sog. „KI-Agent“ wird trainiert, der dann im Betrieb Empfehlungen zur energieoptimalen und prozesssicheren Systembedienung gibt. Als Projektziel entsteht eine Lösung, die Produzenten ohne kapitalintensive Anlagen oder Anlagenerweiterungen sowie Produktivitätsverlust zur Energieeinsparung befähigt. Am Ende steht für das einzelne Werk eine Software, die in Echtzeit die Autoklavenbedienung unterstützt. Neben der Vorhersage realer Härtezeiten werden Empfehlungen für die energieoptimale und prozesssichere Bedienung des Härteprozesses gegeben. Im Erfolgsfall kann das KS-Werk ohne Produktivitätsverlust Energie und CO2 bei der Autoklavierung einsparen. Ein formalisierter Prozess erlaubt die einfache Übertragung auf weitere Werke. Der Transfer erfolgt über mehrere Maßnahmenpakete (Seminare, Beratung, Fachveröffentlichungen, Tagungen und Kongresse, etc.).
Der Lehrstuhl FAPS bringt seine Kompetenzen insbesondere bei tiefgehenden Problemstellungen im Bereich des Machine Learnings ein und übernimmt die Führung in den zugehörigen Arbeitspaketen der Datenvorverarbeitung und der Entwicklung eines Optimierungsagenten zur Unterstützung einer energieoptimalen Autoklavierung.
SIMON: Pneumatische Schaltschrank-Intralogistik und optische MONtageassistenz
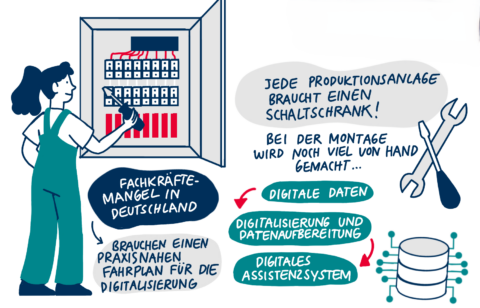
Beim Projekt “SIMON” handelt es sich um einen Innovationssprint im Rahmen des Datipilot-Programmes des BMBF. Gemeinsam mit dem Projektpartner “Rittal GmbH & Co. KG” soll die Effizienz und die Digitalierung im Schaltschrankbau gesteigert werden und die Standortattraktivität Deutschland auch für die manuellen Verdrahtungstätigkeiten erhalten bleiben. Das Projekt zielt darauf ab, ein ganzheitliches Werkerassistenzsystem für die Branche des Schaltschrankbaus zu gestalten. Die angestrebte Lösung basiert auf zwei technologischen Innovationen (1 und 2) und einem holistischen Gesamtziel (3):
- Prozesssicherer und energieeffizienter pneumatischer Transport von konfektionierten Kabeln
- Visuelle Darstellung von Verdrahtungs- und Montageinformationen auf der Montageplatte
- Integriertes Assistenzsystem mit vollautomatisierter Datenableitung
Teilprojekt Lehrstuhl FAPS
Das Teilprojekt des Lehrstuhl FAPS fokussiert die Erarbeitung theoretischer Grundlagen der technologischen Innovationen. Dazu werden neben einem theoretischen, analytischen Modell auch komplexe Simulationen aus Kombination von Computational Fluid Dynamics (CFD) und Discrete Element Method (DEM) für den pneumatischen Transport von biegeschlaffen Bauteilen entwickelt und validiert. Dadurch lassen sich energetische Optimierung insbesondere mit Hinblick auf den Druckluftverbrauch realisieren und die Erkenntnisse werden direkt in das Werkerassistenzsystem integriert.
Zur Visuellen Darstellung liefert der Lehrstuhl zunächst einen Ablauf zur automatisierten Datenaufbereitung von Schaltschrankkomponenten. Dazu wird Künstliche Intelligenz (KI) eingesetzt, um 3D-Daten semantisch aufzubereiten und notwendige Informationen, wie beispielsweise die Position und Ausrichtung einer Eingangsklemme, zu ermitteln. Ferner wird es mit diesen Bauteilinformationen möglich sein, mit einer ausgewählten Visualisierungstechnologie die zu verdrahtenden Klemmen zielgenau anvisieren zu können.
Im Kontext des Gesamtziels entwickelt der Lehrstuhl ein Gesamtkonzeptes für den vollständig automatisierten Datenfluss. Dadurch wird es möglich sein, dass Werkerassistenzsystem ausschließlich mit bestehenden Daten aus dem Schaltschrank-Engineering und den Bauteildaten zu versorgen, um die Assistenzstrategie, Intralogistik und Visualisierung ausführen zu können.
Ziele des Lehrstuhl FAPS
Der Lehrstuhl FAPS wird zum Erreichen der drei übergeordneten Ziele die im Folgenden dargestellten Arbeitsziele fokussieren und erreichen.
- Prozesssicherer und energieeffizienter pneumatischer Transport von konfektionierten Kabeln
- Aufstellung eines theoretischen Modells für die analytische Annährung des Transportverhaltens konfektionierter Kabel
- Aufbau und Validierung eines Simulationsmodells des Transportverhaltens zur energetischen Optimierung des Intralogistiksystems
- Visuelle Darstellung von Verdrahtungs- und Montageinformationen
- Entwicklung und Validierung einer Methodik zur automatisierten, semantischen Aufbereitung von CAD-Daten und 3D-Scan Punktewolken
- Integriertes Assistenzsystem mit vollautomatisierter Datenableitung
- Entwicklung eines Konzeptes für den vollständig automatisierten Datenfluss
Ziele der Rittal GmbH & Co. KG
Die Fa. Rittal wird sich zum Erreichen der übergeordneten Ziele auf die experimentelle Validierung sowie die nutzerzentrierte Entwicklung des Assistenzsystems konzentrieren.
- Prozesssicherer und energieeffizienter pneumatischer Transport von konfektionierten Kabeln
- Experimentelle Validierung
- Visuelle Darstellung von Verdrahtungs- und Montageinformationen
- Auswahl und Adaption einer anwendernahen Visualisierungstechnologie zur Darstellung der notwendigen Informationen
- Integriertes Assistenzsystem mit vollautomatisierter Datenableitung
- Anwendernahe Entwicklung der Softwarelösung zur Visualisierung
- Integration aller Teilsysteme in einem Montagearbeitsplatz mit Anschluss an das pneumatische Intralogistiksystem
Anwendungsnähe
Aufgrund des Charakters des Innovationssprints ist das Forschungsvorhaben sehr anwendungsnah konzipiert. Der direkte Transfer von Ergebnissen in die Industrie hat dabei oberste Priorität und wird durch projektbegleitende Anwenderworkshops und durch einen daraus resultierenden Leitfaden zur Implementierung des Werkerassistenzsystems realisiert. Interessierte Schaltschrankbauer sind herzlich eingeladen zu partizipieren und profitieren an und von anwendungsorientierter Forschung. Kommen Sie einfach auf die genannten Ansprechparter zu!
Die Anmeldephase zum ersten Anwenderworkshop ist gestartet! Hier finden Sie alle Details zur Veranstaltung.
XR-Upskill – Aus- und Weiterbildung mit Extended Reality
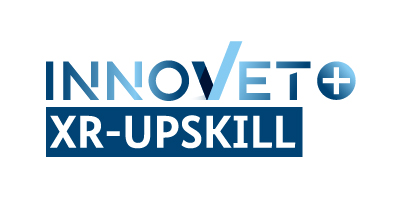
Herausforderung
Der technologische Wandel und die demografische Entwicklung stellen Lehrende und Lernende in Konzernen und kleinen und mittleren Unternehmen (KMU) gleichermaßen vor neue Herausforderungen. Um im Wettbewerb zu bestehen, kommt der Aus- und Weiterbildung eine existenzielle Bedeutung für die Zukunftsfähigkeit ganzer Branchen zu. Um diesen Wandel aktiv gestalten zu können, müssen Auszubildende und Facharbeiter mit neuen zielgruppen- und bedarfsgerechten sowie zeitgemäßen Konzepten qualifiziert werden. Das Projekt XR-Upskill möchte zukünftigen technologischen Herausforderungen mit technologisch neuen Lehr- und Lernmethoden begegnen.
Lösung
Das Projekt erprobt daher den Einsatz innovativer, immersiver Technologien für die Aus- und Weiterbildung anhand konkreter Anwendungsfälle: Hierzu wird ein Extended-Reality-Tool erweitert, das Virtual Reality (VR), Augmented Reality (AR), Mixed Reality (MR) und Spatial Computing (SC) miteinander verknüpft. Dadurch sollen Lerninhalte besser in die berufliche Praxis integriert werden können.
Das Projekt entwickelt zunächst Lerninhalte für Anwendungsfälle in der Automobilindustrie Süddeutschlands, die von strukturellem und technologischem Wandel in besonderer Weise betroffen ist. Die Lerninhalte werden mit Auszubildenden und Fachkräften erprobt. Betriebliches Ausbildungspersonal wird außerdem für den Einsatz von XR-Technologie qualifiziert.
Anschließend ermittelt das Projektteam weitere Anwendungsfälle und teilt die dabei gewonnenen Erkenntnisse im Netzwerk mit KMU, Start-Ups und Berufsschulen sowie weiterführenden Schulen.
Transfer
Ein Fachbeirat stellt die nutzerzentrierte Entwicklung der Inhalte sicher und erarbeitet, welche Voraussetzungen zu schaffen sind, damit VR/AR verbreitet und dauerhaft in die Berufsausbildung integriert werden kann. Im Rahmen des Projekts werden Lizenz-, Nutzungs- und Geschäftsmodelle erarbeitet, damit Projektpartner und Außenstehende nach Projektende die erarbeiteten Lösungen weiterverwenden können. Die Verbundpartner planen die Ergebnisse nach Projektende weiter zu nutzen.
Für den Transfer in andere Regionen, Branchen und in die Berufsbildungspolitik steht eine Vielzahl von Netzwerken zur Verfügung. Darüber hinaus fließen Erkenntnisse des Projekts in die Weiterentwicklung des Ausbildungsberufs „Gestalter/-in für immersive Medien“ ein.
Aktuelle Updates
LinkedIn
test
Adaptive und benutzerfreundliche Kollaboration von Menschen und autonomen mobilen Robotern durch kontinuierlich lernende Algorithmen
Die Adaption und Inbetriebnahme eines autonomen mobilen Roboters für neue bzw. veränderte Arbeitsabläufe und Umgebungen verursacht einerseits Kosten durch die notwendige Beauftragung von Experten und kann andererseits dazu führen, dass der Roboter zeitweise nicht vollumfänglich einsetzbar ist.
Das Forschungsvorhaben KoLAMeRo erarbeitet und demonstriert Lösungsansätze, wie diese Hürden mittels des Einsatzes von automatisierten kontinuierlichen Lernverfahren überwunden werden können.